1. Introduction
Welcome to the world of HEPA Seal Bag-In/Bag-Out Contamination Systems! In this chapter, we will embark on a journey to understand the essence of these systems and delve into why their proper operation and maintenance are paramount.
1.1. Overview of HEPA Seal Bag-In/Bag-Out Contamination Systems
HEPA Seal Bag-In/Bag-Out (BIBO) Contamination Systems represent a cutting-edge solution in the realm of air filtration technology. These systems are meticulously designed to safeguard both facility personnel and the general public from hazardous materials by efficiently filtering out these potentially harmful substances.
Benefits of HEPA Seal BIBO Systems
- Enhanced safety: Minimizes exposure to dangerous contaminants during filter replacement.
- Versatile applications: Suitable for industries and research facilities handling toxic, biological, or carcinogenic materials.
- Consistent procedure: Regardless of the filter type, the filter change-out process remains consistent.
HEPA Seal BIBO systems are at the forefront of protecting the environment and human health, offering a level of safety and efficiency that is second to none.
1.2. Importance of Proper Operation and Maintenance
While the concept of HEPA Seal BIBO systems is revolutionary, their effectiveness hinges on the meticulous adherence to proper operation and maintenance procedures. Your chief safety officer’s amendments and manufacturer’s instructions play a pivotal role in ensuring the highest level of protection.
Your Safety, Our Priority
- Safety protocols: Comprehensive guidelines provided to minimize the risk of contamination.
- Equipment readiness: Having the necessary tools and equipment on hand before starting work.
- The Filtration Group method: A detailed explanation of the banding method of sealing the bag for utmost safety.
Remember, the goal is to prevent both yourself and the immediate environment from being contaminated with the materials captured on the dirty filter. Your journey into the world of HEPA Seal BIBO Contamination Systems begins here, with a commitment to safety and efficiency.
2. Manufacture’s Message
In the world of YOUTH Tech., where innovation meets safety, understanding the purpose of HEPA Seal Bag-In/Bag-Out (BIBO) Housings is the cornerstone of successful operation. Join us in this chapter as we delve into the manufacturer’s message and unravel the essential aspects of these cutting-edge containment systems.
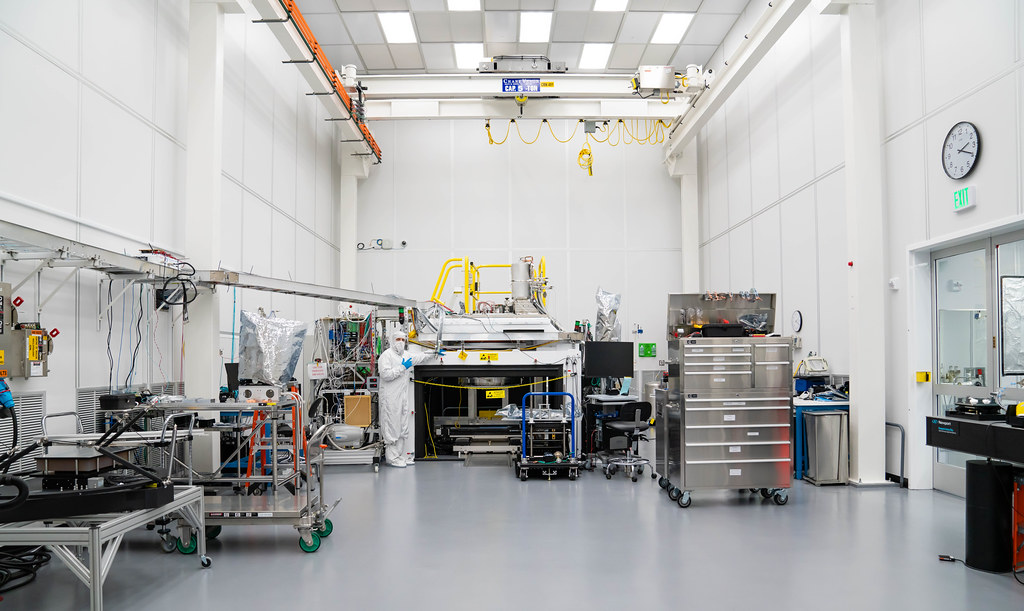
2.1. Understanding the Purpose of HEPA Seal Bag-In/Bag-Out Housings
HEPA Seal BIBO Housings, often referred to as Bag in Bag out HEPA Filter systems, are engineered to serve a critical role in maintaining a contamination-free environment. At their core, these systems are designed to protect personnel and the environment by effectively filtering out hazardous materials.
A Glimpse into the Purpose
- Protection: The primary goal is to shield individuals and the surroundings from harmful contaminants during filter replacement.
- Adaptability: These systems cater to a range of applications, making them indispensable in industries and research facilities dealing with toxic, biological, or carcinogenic substances.
- Uniform Procedure: Regardless of the specific filter type, the procedure for changing filters remains consistent, ensuring reliability.
HEPA Seal BIBO systems are more than just filtration; they are a testament to advanced technology meeting stringent safety requirements.
2.2. Safety Precautions and Chief Safety Officer’s Amendments
In this era of technological advancement, safety remains paramount. HEPA Seal BIBO systems demand meticulous adherence to safety precautions and the guidance of the chief safety officer to ensure optimal performance and protection.
3. Introduction to HEPA Seal Bag-In/Bag-Out Housings
Welcome to the world of Bag in Bag out HEPA Filters, where innovation meets safety in YOUTH Tech. In this chapter, we’ll explore the exciting features and benefits of Bag-In/Bag-Out (BIBO) Filter Housings and discover the diverse applications they serve in industries and research facilities.
3.1. Features and Benefits of Bag-In/Bag-Out Filter Housings
Bag-In/Bag-Out Filter Housings are at the forefront of modern contamination control. Let’s dive into their remarkable features and the multitude of benefits they bring to the table:
Cutting-Edge Features
- Ribbed Bag-In/Bag-Out Ring: A distinguishing feature that ensures safe filter replacement.
- Versatile Filter Arrangements: Accommodates various filter types, including prefilters, HEPA filters, and more.
- Uniform Procedure: Regardless of filter variations, the change-out procedure remains consistent.
Unveiling the Benefits
- Contaminant Isolation: Effectively isolates hazardous materials during filter replacement, safeguarding personnel and the environment.
- Application Versatility: Ideal for industries handling dangerous, toxic, biological, or carcinogenic substances.
- Efficiency and Reliability: Ensures a reliable and standardized process, reducing the margin for error.
With these impressive features and benefits, Bag-In/Bag-Out Filter Housings are revolutionizing the way we approach contamination control.
3.2. Applications in Industries and Research Facilities
The applications of Bag-In/Bag-Out systems extend far and wide, making them a vital component in various industries and research settings. Let’s explore the diverse domains where these systems play a pivotal role:
Industries at the Forefront
- Pharmaceutical: Ensuring the safety of personnel handling potent drug compounds.
- Nuclear: Safeguarding against radioactive materials during filter replacement.
- Biotechnology: Protecting against biological contaminants in research and production.
Research Facilities Advancing Science
- Laboratories: Maintaining a contamination-free environment for sensitive experiments.
- Healthcare: Ensuring air purity in critical areas like operating rooms and isolation units.
- Cleanrooms: Crucial for semiconductor manufacturing and precision engineering.
As we step into these industries and research facilities, Bag-In/Bag-Out systems continue to redefine safety standards and contamination control. Join us on this remarkable journey of discovery and innovation.
4. Fluid Seal Design Concept
In the realm of Bag in Bag out HEPA Filter systems, the fluid seal design concept stands as a cornerstone of safety and efficiency. In this chapter, we delve deep into how this innovative mechanism works, focusing on the intricate details of the fluid seal, the locking mechanism, and the knife-edge seal.
4.1. How Fluid Seal Works in Bag-In/Bag-Out Housings
At the heart of every Bag-In/Bag-Out (BIBO) system lies the fluid seal, a robust mechanism that ensures the containment of hazardous materials during filter change-outs. Let’s dissect the workings of this ingenious system:
Fluid Seal Operation
- Sealing Action: As the filter is removed, the fluid seal activates, preventing any potential escape of contaminants.
- Pressure Differential: Maintains a controlled environment by managing pressure differentials.
- Seamless Transition: Ensures a smooth transition from a contaminated filter to a new one.
Key Components
- Sealing Gasket: Forms an airtight seal between the housing and the filter.
- Knife-Edge Seal: An integral part of the mechanism, it enhances the sealing effect.
- Fluid Tight Compartment: Guarantees complete containment, safeguarding personnel and the surroundings.
4.2. Locking Mechanism and Knife-Edge Seal
The locking mechanism in a Bag-In/Bag-Out housing plays a pivotal role in maintaining the integrity of the fluid seal. Let’s explore the intricacies of this mechanism:
Locking Mechanism
- Safety First: Designed with safety as the foremost priority to prevent accidental filter release.
- User-Friendly: Simple yet effective, allowing for easy filter replacement while ensuring safety.
- Reliable Engagement: Locks the filter securely in place, eliminating the risk of breaches.
The Knife-Edge Seal
- Enhanced Seal: The knife-edge seal complements the fluid seal, adding an extra layer of protection.
- Optimal Contact: Ensures that the seal remains intact under varying pressure conditions.
- Durable Design: Engineered for long-lasting performance and minimal maintenance.
As we unravel the complexities of the fluid seal design concept, you’ll gain a profound understanding of its significance in Bag-In/Bag-Out systems. Join us in the next chapter as we explore the description of the fluid seal filter locking system, delving even deeper into the inner workings of this remarkable technology.
5. Description of Fluid Seal Filter Locking System
In the dynamic landscape of Bag in Bag out HEPA Filter systems, understanding the intricacies of the fluid seal filter locking system is crucial. This chapter takes an in-depth look at the internal filter-locking arm operation and the steps to ensure proper engagement for safety.
5.1. Internal Filter-Locking Arm Operation
The internal filter-locking arm is the linchpin of the fluid seal filter locking system, ensuring the integrity of the containment process. Here’s how it operates:
Mechanism Overview
- Synchronized Movement: The locking arm moves in sync with the filter change-out process, guaranteeing a secure connection.
- Positive Locking: Engages firmly with the filter, preventing any unintentional release.
- Redundant Safety: A fail-safe design adds an extra layer of protection against accidental disengagement.
User-Friendly Design
- Ease of Use: Designed for simplicity, allowing operators to change filters efficiently.
- Visual Confirmation: Provides visual cues to ensure proper locking, reducing the chance of errors.
- Maintenance-Friendly: Minimal maintenance requirements for long-term reliability.
5.2. Ensuring Proper Engagement for Safety
Proper engagement of the internal filter-locking arm is paramount to the safety of both personnel and the environment. Here are the steps to guarantee this crucial aspect:
Pre-Engagement Checks
- Visual Inspection: Inspect the locking arm for any signs of damage or wear before use.
- Alignment Verification: Ensure the arm is properly aligned with the filter and housing.
- Secure Lubrication: Lubricate moving parts according to manufacturer recommendations.
Engagement Process
- Smooth Movement: Activate the arm smoothly, following prescribed procedures.
- Positive Feedback: Listen for audible clicks or feel for tactile feedback to confirm secure engagement.
- Visual Confirmation: Verify that the arm is securely locked in place.
Post-Engagement Verification
- Testing Procedures: Conduct leak tests or pressure differential tests to validate the seal.
- Periodic Inspections: Regularly inspect the locking arm during routine maintenance.
- Documentation: Maintain records of engagement for compliance and audit purposes.
By comprehending the inner workings of the fluid seal filter locking system and the steps to ensure proper engagement, you can effectively contribute to the safety and efficiency of Bag in Bag out HEPA Filter systems.
Join us in the next chapter as we dive into the gasket seal design concept, shedding light on the role of pressure bars, springs, and clamping load in maintaining the integrity of these systems.
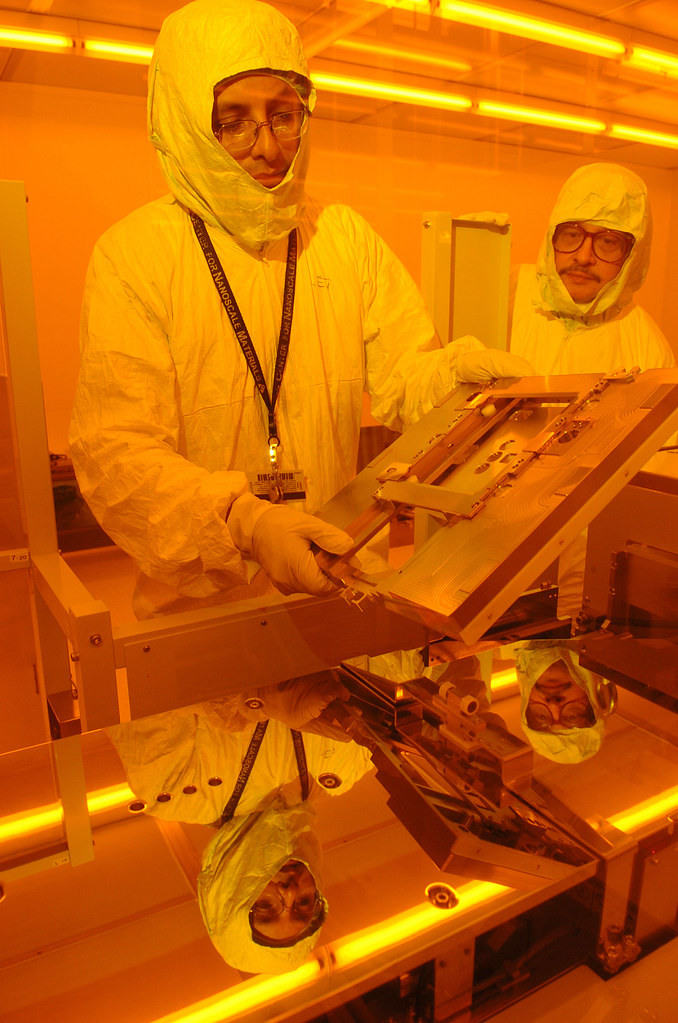
6. Gasket Seal Design Concept
In the intricate world of Bag in Bag out HEPA Filter systems, the gasket seal design concept plays a pivotal role in ensuring airtight integrity. This chapter explores the fundamental principles of the gasket seal mechanism and the critical components involved, including pressure bars, springs, and clamping load.
Understanding Gasket Seal Mechanism
The gasket seal mechanism forms the heart of the Bag in Bag out HEPA Filter system, sealing the filter housing to prevent any contaminant escape. Here’s a closer look at how it operates:
Sealing Material
- High-Quality Materials: Gasket seals are typically made from materials like silicone, neoprene, or fluoropolymer, chosen for their durability and resistance to chemicals.
- Compression Design: The gasket is designed to compress tightly when the housing is sealed, forming an airtight barrier.
Role of Pressure Bars
- Uniform Pressure: Pressure bars are strategically placed along the gasket to ensure even pressure distribution.
- Prevent Leaks: Pressure bars help maintain consistent contact between the gasket and housing, minimizing the risk of leaks.
Springs in the System
- Compliance and Flexibility: Springs provide the necessary compliance and flexibility to accommodate variations in housing and filter dimensions.
- Constant Tension: They help maintain constant tension on the gasket, compensating for any settling or shifting.
Pressure Bars, Springs, and Clamping Load
The effectiveness of the gasket seal design concept relies on the careful coordination of pressure bars, springs, and clamping load:
Pressure Bars’ Role
- Secure Contact: Pressure bars ensure a secure, uniform contact between the gasket and housing.
- Sealing Performance: They play a vital role in the overall sealing performance, preventing contaminants from escaping.
Influence of Springs
- Adjustability: Springs can be adjusted to achieve the optimal tension required for a reliable seal.
- Dynamic Response: They respond to changes in filter and housing conditions, maintaining the seal’s integrity.
Clamping Load
- Controlled Force: Clamping load refers to the force applied to compress the gasket.
- Critical Balance: Achieving the right balance of clamping load is essential for an effective seal without damaging components.
Understanding the gasket seal design concept and the role of pressure bars, springs, and clamping load is paramount for maintaining the integrity of Bag in Bag out HEPA Filter systems.
Join us in the next chapter as we delve into the crucial aspects of handling and storing filter elements, exploring various types of particulate filters and the best practices for their preservation.
7. Handling and Storage of Filter Elements
When it comes to Bag in Bag out HEPA Filter systems, the handling and storage of filter elements are of utmost importance to ensure their optimal performance. In this chapter, we will explore the various aspects of handling and storing particulate filters, including different types of filters, best practices for handling, and manufacturer’s recommendations.
Types of Particulate Filters
Before delving into the handling and storage practices, let’s first understand the different types of particulate filters commonly used in Bag in Bag out HEPA Filter systems:
1. HEPA Filters
- High-Efficiency: High-Efficiency Particulate Air (HEPA) filters are known for their exceptional ability to capture particles as small as 0.3 microns.
- Critical Application: They are widely used in applications where maintaining air purity is crucial, such as healthcare facilities, cleanrooms, and laboratories.
2. ULPA Filters
- Ultra-Low Penetration Air: ULPA filters offer an even higher level of filtration, capturing particles down to 0.12 microns.
- Specialized Applications: ULPA filters are often employed in ultra-clean environments like semiconductor manufacturing and pharmaceutical production.
3. Pre-Filters
- Initial Filtration: Pre-filters are used as the first line of defense in removing larger particles and contaminants before the air passes through the main HEPA or ULPA filters.
- Extended Filter Life: They help extend the lifespan of the more expensive HEPA or ULPA filters by capturing larger particles.
Proper Handling and Storage Practices
Maintaining the integrity of particulate filters is essential to ensure the efficiency of Bag in Bag out HEPA Filter systems. Here are some best practices for handling and storing filter elements:
1. Gentle Handling
- Avoid Impact: Filters should be handled gently to prevent any physical damage that could compromise their effectiveness.
- Use Proper Tools: When moving or installing filters, use appropriate tools to minimize contact with the filter media.
2. Clean Environment
- Dust-Free Area: Filters should be handled in a clean and dust-free environment to prevent contamination.
- Storage Conditions: Filters should be stored in a dry, cool, and clean location to avoid exposure to moisture or pollutants.
3. Inspection
- Regular Inspection: Filters should be inspected regularly for any visible damage, tears, or signs of wear.
- Replace as Needed: Damaged filters should be replaced promptly to maintain the system’s performance.
Shelf Life and Manufacturer’s Recommendations
Particulate filters have a shelf life, and it’s crucial to adhere to the manufacturer’s recommendations regarding storage duration. The shelf life can vary depending on factors such as filter type and environmental conditions.
Manufacturers often provide guidelines on storage duration and conditions, and it’s essential to follow these recommendations to ensure that the filters perform optimally when needed.
Proper handling and storage of filter elements are essential steps in maintaining the efficiency and longevity of Bag in Bag out HEPA Filter systems. By following these best practices and manufacturer’s recommendations, you can ensure that your filters are ready to perform their vital role in maintaining air quality.
In the next chapter, we will shift our focus to the installation of new housings, covering the critical steps involved in positioning, mounting, and preparing the ductwork for your Bag in Bag out HEPA Filter system.
8. Installation of New Housings
As we continue our journey into the world of Bag in Bag out HEPA Filter systems, it’s time to explore the critical chapter on the installation of new housings. Properly positioning and mounting the housing, cleaning and preparing the ductwork, and installing filters are essential steps in ensuring the efficiency and effectiveness of your Bag in Bag out HEPA Filter system.
8.1. Positioning and Mounting the Housing
Precision is Key
When it comes to positioning the housing for your Bag in Bag out HEPA Filter system, precision is key. Proper alignment ensures that the system operates at its peak performance.
Key Considerations:
- Location Selection: Choose a location that allows easy access for maintenance and filter replacement.
- Alignment: Ensure that the housing is level and plumb for optimal performance.
- Secure Mounting: Securely mount the housing to prevent vibrations or movement that could impact the system.
8.2. Cleaning and Preparing Ductwork
Clean Ductwork, Clean Air
Clean ductwork is essential to maintain air quality and system efficiency. Before installation, thorough cleaning and preparation are necessary.
Steps to Follow:
- Duct Inspection: Inspect ducts for any debris, dust, or obstructions.
- Cleaning: Clean ducts using appropriate methods and tools to remove any contaminants.
- Sealing: Ensure that all duct joints are properly sealed to prevent air leakage.
8.3. Installing Filters and Performing Leak Tests
Filters: The Heart of the System
Properly installing filters is crucial to the functionality of your Bag in Bag out HEPA Filter system. Additionally, conducting leak tests is a vital step in verifying the system’s integrity.
Installation Guidelines:
- Filter Orientation: Ensure filters are installed in the correct orientation as per manufacturer instructions.
- Sealing: Properly seal the filters to prevent bypass air.
- Leak Tests: Perform leak tests using appropriate methods to verify system integrity.
With the housing in place, ductwork prepared, and filters installed, your Bag in Bag out HEPA Filter system is one step closer to being fully operational. In the next chapter, we will guide you through the start-up procedures, covering everything from shutdown and airflow control to job safety analysis and the step-by-step filter change-out process. Stay tuned for more insights into maximizing the efficiency and safety of your system.
9. Start-Up Procedures
In the realm of Bag in Bag out HEPA Filter systems, successful start-up procedures are the cornerstone of efficient and safe operation. This chapter delves into the intricacies of this critical phase, ensuring that your system functions optimally from the moment it’s initiated.
9.1. Shutdown and Airflow Control
The First Steps
Before you begin the start-up process, a proper shutdown is essential. Ensuring that the system is at a complete standstill is the first step in this journey. Once shutdown is confirmed, attention must shift to airflow control.
Key Aspects:
- Shutdown Sequence: Follow manufacturer guidelines for a systematic shutdown process.
- Airflow Control: Carefully control airflow parameters to maintain system integrity.
- Verification: Confirm that the system has stopped completely before proceeding.
9.2. Job Safety Analysis and Personal Protective Equipment
Safety First
Safety is paramount during start-up procedures. Conducting a comprehensive job safety analysis (JSA) is a non-negotiable step to identify and mitigate potential risks. Furthermore, the correct use of personal protective equipment (PPE) is crucial to protect personnel.
Steps to Take:
- JSA: Analyze every aspect of the start-up process to identify potential hazards.
- Risk Mitigation: Develop strategies to minimize risks and ensure safety.
- PPE Usage: Ensure that all personnel involved are equipped with the appropriate PPE.
9.3. Cleaning and Providing New Filters
Fresh Filters, Clean Air
To guarantee the optimal performance of your Bag in Bag out HEPA Filter system, it’s essential to clean the system thoroughly and provide it with new filters.
Necessary Actions:
- System Cleaning: Remove any residual contaminants or particles from the system.
- Filter Replacement: Install new filters as per manufacturer specifications.
- Sealing: Ensure that the filters are securely sealed to prevent air bypass.
9.4. Step-by-Step Filter Change-Out Process
A Methodical Approach
The step-by-step filter change-out process is a highly regulated procedure. Following each step meticulously is vital to maintain system integrity and safety.
Guiding Steps:
- Preparation: Gather all necessary tools and equipment.
- Isolation: Ensure that the system is isolated from any external airflow.
- Filter Removal: Carefully remove old filters, paying attention to any potential contaminants.
- Filter Installation: Place new filters following the correct orientation.
- Sealing: Seal the filters appropriately to prevent bypass air.
- Leak Tests: Perform leak tests to verify system integrity.
- Startup: Gradually initiate the system while monitoring performance.
By following these detailed start-up procedures, your Bag in Bag out HEPA Filter system will be ready to fulfill its role efficiently and safely. In our next chapter, we will explore Appendix A, focusing on the importance of providing operating conditions and ensuring satisfactory system performance. Stay tuned to maximize the potential of your system.
10. Appendix A – Operating Conditions
In the world of Bag in Bag out HEPA Filter systems, understanding the importance of providing specific operating conditions is critical to ensuring long-term, efficient, and satisfactory system performance. In this appendix, we delve into the intricacies of maintaining optimal conditions for your Bag in Bag out HEPA Filter system.
10.1. Importance of Providing Operating Conditions
The Backbone of Performance
Operating conditions are the backbone of any Bag in Bag out HEPA Filter system. These conditions encompass a range of factors, including temperature, humidity, airflow rates, and more. Properly maintaining these conditions is vital to ensure that your system functions at its peak.
Key Aspects:
- Temperature Control: Maintain a stable temperature range suitable for the system’s operation.
- Humidity Levels: Ensure that humidity levels are within the recommended range.
- Airflow Rates: Monitor and control airflow rates to match system requirements.
- Pressure Differentials: Maintain appropriate pressure differentials across filters.
10.2. Ensuring Satisfactory System Performance
The Ultimate Goal
The ultimate goal of providing optimal operating conditions is to ensure satisfactory system performance. Without these conditions, the system’s efficiency may suffer, leading to reduced filtration capability and potentially compromising the safety of your facility.
Key Considerations:
- Filter Efficiency: Proper conditions maximize filter efficiency, ensuring the capture of particulate contaminants.
- Energy Efficiency: Maintaining optimal conditions can lead to energy savings and reduce operating costs.
- Longevity: A well-maintained system has a longer lifespan, reducing the need for frequent replacements.
- Safety: Adequate conditions are essential for ensuring the safety of personnel and the environment.
By diligently maintaining the specified operating conditions for your Bag in Bag out HEPA Filter system, you can achieve the highest level of performance, efficiency, and safety. This concludes our exploration of Appendix A. In our next chapter, we will delve into Appendix B, where we discuss safety precautions for locking tray change-out and the methods involved. Stay tuned to enhance your understanding of this critical aspect of Bag in Bag out HEPA Filter systems.
11. Appendix B – Locking Tray Change Out
In this appendix, we explore essential safety precautions and methods for replacing locking trays in Bag in Bag out HEPA Filter systems. Safety is paramount, and understanding the proper procedures is crucial to maintain the integrity of the containment system.
11.1. Safety Precautions for Locking Tray Change Out
Prioritizing Safety
Before embarking on the replacement of locking trays, it is vital to prioritize safety. This includes:
- Training: Ensure that personnel involved in the procedure are well-trained and knowledgeable about safety protocols.
- Personal Protective Equipment (PPE): Provide the necessary PPE, including gloves, masks, and eyewear, to protect against potential exposure.
- Area Preparation: Isolate the work area and post warning signs to prevent unauthorized access.
- Emergency Procedures: Establish clear emergency response procedures in case of unforeseen issues.
11.2. Fluid Seal Method for Replacing Locking Trays
The Fluid Seal Approach
The fluid seal method for replacing locking trays is a well-established technique used in Bag in Bag out HEPA Filter systems. It involves the following steps:
- Isolate and Shut Down: Ensure that the system is isolated and safely shut down before initiating any work.
- Depressurize: Release any pressure within the system to prevent sudden releases of potentially harmful substances.
- Fluid Seal Activation: Activate the fluid seal mechanism to secure the tray being replaced.
- Tray Removal: Carefully remove the locking tray, ensuring it is free from contaminants.
- Replacement: Install the new tray securely, ensuring proper alignment.
- Fluid Seal Deactivation: Deactivate the fluid seal mechanism once the new tray is in place.
- Testing: Conduct thorough testing to ensure the system is functioning correctly.
- Safety Check: Perform a final safety check to verify that all procedures have been executed correctly.
11.3. Gasket Seal Method for Replacing Locking Trays
The Gasket Seal Approach
An alternative method for replacing locking trays is the gasket seal approach. This method offers a different set of advantages and is employed as follows:
- Isolate and Shut Down: As with the fluid seal method, start by isolating and shutting down the system.
- Depressurize: Release any pressure within the system to ensure safety.
- Gasket Seal Inspection: Check the gasket seal for any signs of wear or damage.
- Tray Removal: Carefully remove the old locking tray.
- Gasket Replacement: If necessary, replace the gasket seal to maintain a tight and secure fit.
- Tray Installation: Install the new locking tray, ensuring it is properly seated.
- Testing: Conduct thorough testing to verify the system’s functionality.
- Safety Checks: Perform a final safety check to confirm that all steps have been carried out correctly.
By adhering to these safety precautions and selecting the appropriate method for replacing locking trays in Bag in Bag out HEPA Filter systems, you can ensure the integrity and safety of your containment system. In the next chapter, we will conclude our comprehensive exploration of Bag in Bag out HEPA Filter systems.
12. Conclusion
As we conclude our comprehensive exploration of Bag in Bag out HEPA Filter systems, it’s essential to recap the key points and emphasize the importance of adhering to safety procedures. Throughout this article, we’ve delved into various aspects of these systems, from their design concepts to installation, operation, and maintenance.
12.1. Recap of Key Points
Let’s briefly revisit the critical takeaways from our discussion:
- Overview: Bag in Bag out HEPA Filter systems, also known as BIBO systems, are essential for containing hazardous materials in various industries.
- Safety: Safety should always be the top priority when working with these systems, from the initial installation to maintenance and filter change-outs.
- Design Concepts: We explored both fluid seal and gasket seal design concepts and their significance in maintaining containment.
- Proper Handling: Proper handling and storage of filter elements are crucial to ensure their effectiveness and longevity.
- Installation: The correct installation of new housings involves positioning, mounting, ductwork preparation, and thorough leak tests.
- Start-Up Procedures: Understanding shutdown, airflow control, job safety analysis, and personal protective equipment is vital during system start-up.
- Operating Conditions: Providing and maintaining suitable operating conditions is essential for optimal system performance.
- Locking Tray Change Out: We discussed safety precautions and methods for replacing locking trays, including the fluid seal and gasket seal approaches.
12.2. Importance of Adhering to Safety Procedures
In the world of Bag in Bag out HEPA Filter systems, safety is non-negotiable. These systems are often used in environments where the containment of hazardous materials is critical, making the adherence to safety procedures paramount. Failure to follow safety protocols can have severe consequences, including exposure to dangerous substances and potential system failures.
By investing in comprehensive training, appropriate personal protective equipment, and meticulous adherence to safety guidelines, you can ensure the well-being of your personnel and the reliability of your containment system. Safety is not just a checklist but a commitment to protecting lives and preserving the integrity of your operations.
In conclusion, Bag in Bag out HEPA Filter systems, with their innovative design concepts and rigorous safety standards, play a vital role in various industries. Proper operation and maintenance are essential to reap the benefits of these systems fully.
We hope this article has provided valuable insights into the world of Bag in Bag out HEPA Filter systems and their critical role in maintaining safety and containment. As you implement these practices, always remember that safety should be at the forefront of every action in your YOUTH Tech. facility.
Thank you for joining us on this journey of discovery, and we wish you success in your endeavors with Bag in Bag out HEPA Filter systems.
FAQs
- How do BIBO systems protect against hazardous materials? HEPA Seal Bag-In/Bag-Out (BIBO) systems provide protection by filtering and containing hazardous materials within the housing. The filters inside the system capture dangerous substances, preventing their release into the environment. The Bag-In/Bag-Out method ensures that contaminated filters are safely removed and replaced without any direct contact, minimizing the risk of exposure.
- What is the difference between fluid seal and gasket seal designs? The main difference lies in how the seal is achieved. In fluid seal designs, a continuous knife-edge inside the housing mates with a gel-filled perimeter channel on the filter, creating a seal when the locking mechanism forces the filter against the knife-edge. Conversely, gasket seal designs utilize a continuous flat mounting surface inside the housing that mates with a perimeter gasket on the filter. The locking mechanism, through pressure bars and springs, compresses the gasket against the mounting surface to create a seal.
- What precautions should be taken when handling filter elements? Handling filter elements, especially high-efficiency filters like HEPA filters, requires care. Filters should be stored in clean, controlled environments within specific temperature and humidity ranges. Stacking filters should be avoided to prevent damage. During handling, use appropriate personal protective equipment and avoid touching the filter media directly, ensuring the filters remain free from contamination.
- Why is a thorough job safety analysis essential during start-up procedures? A comprehensive job safety analysis is vital during start-up procedures to identify potential hazards and risks associated with filter installation or removal. It helps ensure that safety measures are in place, personnel are wearing the necessary personal protective equipment, and that the system is properly shut down to prevent accidents, exposure to contaminants, and system damage.
- How can non-factory alterations affect the BIBO system’s performance? Non-factory alterations to the BIBO system can compromise its integrity and performance. Any changes made outside of manufacturer specifications may lead to leaks, improper filter sealing, or reduced system efficiency. It is essential to consult with the manufacturer and follow their guidelines to maintain the system’s safety and effectiveness.
Related Contents:
- Understanding YOUTH’s Bag-In-Bag-Out (BIBO) Systems: Ensuring Safety and Clean Air
- What are Gel Seal Mini-Pleat HEPA Filters and How to Make the Right Choice?
- Installation, Operation, and Maintenance of Cleanroom Equipment: A Comprehensive Guide
- The Comprehensive Guide to Bag-in-Bag-Out (BIBO) HEPA Filter Replacement
- The Ultimate Guide to YOUTH’s Bag-In-Bag-Out (BIBO) HEPA Filter Replacement
- Understanding YOUTH HEPA Housing Boxes for Cleanroom Environments
- Bag In, Bag Out Changeout Procedure for Safe Change Housings – YOUTH Air Tech
- The Ultimate Guide to YOUTH’s HEPA Housing Box: Ensuring Impeccable Cleanroom Air Quality
- The Ultimate Guide to YOUTH’s Bag-In-Bag-Out (BIBO) Systems: Ensuring Safety and Clean Air