Understanding Bag In Bag Out (BIBO) Systems
Bag In Bag Out (BIBO) systems represent the gold standard in contamination control technology for critical environments where hazardous particulates, biological agents, or other harmful substances must be completely contained during filter maintenance operations. These specialized filtration housings incorporate a unique mechanism that allows filter replacement without direct contact between maintenance personnel and potentially dangerous filter media, significantly enhancing safety protocols and regulatory compliance.
The core principle behind BIBO systems is elegantly simple yet technologically sophisticated: the contaminated filter is sealed within a continuous polymer bag before removal from its housing, creating an unbroken containment barrier between hazardous materials and the surrounding environment. This methodology has revolutionized maintenance procedures in high-containment facilities, transforming what was previously a high-risk operation into a systematically controlled process with quantifiable safety parameters.
Developed initially for nuclear applications in the mid-20th century, BIBO technology has evolved substantially to meet increasingly stringent containment requirements across multiple industries. Today’s systems incorporate advanced materials science, precision engineering, and sophisticated validation protocols to ensure absolute containment integrity under diverse operating conditions. Contemporary BIBO implementations represent the convergence of mechanical engineering excellence, materials innovation, and rigorous safety standards.
The architecture of a modern BIBO system typically comprises several key components:
A robust filter housing constructed from corrosion-resistant materials (typically 304 or 316L stainless steel)
Specialized access ports with contamination-proof sealing mechanisms
Continuous polymer bagging systems with secure fastening capabilities
Pressure differential maintenance systems to ensure directional airflow
Validation ports for performance verification and compliance testing
Integrated monitoring systems for operational parameter tracking
These components work in concert to create a comprehensive containment solution that addresses both immediate safety concerns and long-term regulatory compliance requirements. The engineering principles underlying these systems have been refined through decades of field implementation, resulting in highly reliable containment protocols that can be validated through standardized testing methodologies.
Industry standards governing BIBO systems have evolved significantly, with organizations like the Institute of Environmental Sciences and Technology (IEST), American Society of Mechanical Engineers (ASME), and International Organization for Standardization (ISO) establishing rigorous performance benchmarks. Compliance with standards such as ASME AG-1, ISO 14644, and IEST-RP-CC001 has become essential for facilities implementing BIBO technology, particularly in regulated industries where documentary evidence of containment efficacy is mandated.
The implementation of YOUTH BIBO systems provides organizations with a comprehensively engineered solution to containment challenges, addressing both immediate operational needs and long-term regulatory requirements through tested, validated technology.
Technical Specifications and Design Features
The technical architecture of Bag In Bag Out (BIBO) systems represents a sophisticated engineering approach to absolute containment, with specifications that directly address the most demanding requirements of critical environments. Understanding these technical parameters is essential for procurement teams evaluating implementation options for their facilities.
Housing Construction and Material Composition
BIBO housings are typically fabricated from industrial-grade stainless steel, with 304 and 316L variants being the industry standard for most applications. These materials offer exceptional corrosion resistance, durability under harsh operating conditions, and compatibility with rigorous decontamination protocols. Key specifications include:
Material thickness: 1.5mm to 3.0mm depending on application requirements
Welding specifications: Continuous TIG welding with full penetration
Surface finish options: #2B, #4, or electropolished (Ra 0.5μm or better)
Temperature tolerance: -20°C to 120°C standard range
Pressure rating: Typically ±3000 Pa differential pressure
Leak tightness: Class C according to EN1751 (ISO 10648-2 Class 2 equivalent)
For applications involving aggressive chemicals or unusual environmental conditions, specialized materials including Hastelloy, polypropylene, or fiberglass-reinforced polymers may be specified, though these represent a smaller percentage of implementations.
Containment Mechanism Engineering
The defining feature of BIBO systems is their specialized containment mechanism, comprising several engineered components working in unison:
Safety edge design: Rolled or beaded edges on all contact surfaces to prevent bag tearing
Continuous bag retention bands: Spring-tensioned or mechanical clamping systems
Port design: Tapered access ports with minimum 220mm diameter for standard applications
Gasket materials: Closed-cell neoprene, silicone, or EPDM compounds depending on application
Change-out port covers: Positive-locking mechanisms with compression sealing
These components are precision-engineered to maintain absolute containment during the critical filter replacement process, with multiple redundant systems ensuring that containment integrity is preserved even if a single component fails.
Filtration Performance Parameters
BIBO systems accommodate various filter classifications, with specifications typically including:
Filter Classification | Particle Removal Efficiency | Application Context |
---|---|---|
HEPA (H13) | 99.95% at 0.3μm | General pharmaceutical manufacturing |
HEPA (H14) | 99.995% at 0.3μm | Aseptic processing areas |
ULPA (U15) | 99.9995% at 0.12μm | Microelectronics manufacturing |
ULPA (U16) | 99.99995% at 0.12μm | Critical semiconductor processes |
Nuclear Grade | 99.97% at 0.3μm with DOP testing | Radioactive material handling |
Each classification corresponds to specific industrial applications and regulatory requirements, with filter media, frame construction, and sealant materials varying accordingly.
Pressure Control and Monitoring Systems
Advanced BIBO implementations incorporate sophisticated pressure differential control systems:
Pressure measurement accuracy: ±5 Pa standard
Pressure display: Digital or analog with clearly marked safe operating ranges
Pressure alert systems: Configurable high/low alarms with visual and audible indicators
Monitoring ports: Standardized pressure tap locations upstream and downstream
Connectivity: Analog output (4-20mA) or digital communication (Modbus, BACnet) for BMS integration
These systems ensure that proper directional airflow is maintained during both normal operation and filter change procedures, preventing contaminant migration through precise pressure cascade management.
Validation and Certification Features
Modern BIBO systems include engineered features specifically designed to facilitate validation:
Aerosol injection ports positioned according to IEST-RP-CC034 recommendations
PAO-compatible materials throughout the aerosol path
Challenge port distribution designed for uniform aerosol concentration
Downstream scanning access ports meeting ISO 14644 requirements
Integrated pressure decay test capabilities
Standardized documentation packages for regulatory submission
These features streamline the validation process, significantly reducing the time and resource requirements for initial qualification and periodic recertification.
The comprehensive engineering approach evident in these technical specifications demonstrates the evolution of BIBO technology from its origins as a specialized containment solution to today’s highly refined systems that address multiple aspects of contamination control, regulatory compliance, and operational efficiency.
Variations of BIBO Filter Replacement Procedures

The Bag-in-Bag-Out (BIBO) procedure, primarily associated with the replacement of air filters in situations where the filter contains hazardous contaminants, can vary slightly depending on the industry and specific use case.
Some variations of the BIBO process might include:
- Single Bag BIBO:
The simplest form is where a single bag is used to enclose and remove the contaminated filter from its housing. This method is typically used when the level of containment required is less stringent. - Double Bag BIBO:
A more secure method that involves a second containment layer. The contaminated filter is first placed in one bag, which is then placed inside a second bag, adding an extra level of protection against potential exposure. - Multiple Bag BIBO:
For environments with extremely hazardous materials, multiple bags may be used to ensure the highest levels of containment. Each additional bag provides an extra level of security. - Safety Cabinet BIBO:
This variation includes a safety cabinet or a safe-change housing. The filter is changed inside a containment cabinet with its own built-in BIBO system, further minimizing the risk of exposure. - Custom BIBO Systems:
For unique applications, custom BIBO systems are designed to fit specific requirements. These might include variations in bag materials, housing designs, and sealing mechanisms to address particular contaminants or to fit specialized equipment. - Portable BIBO Units:
Some BIBO systems are designed to be portable, allowing them to be moved to the filter location. This makes them ideal for environments where filters may not be centrally located or easily accessible.
The key aspect of all these types is the ability to safely and effectively isolate the contaminated filter from the surrounding environment and personnel during the change-out process.
Customized BIBO Housing and Unit Solutions
YOUTH is dedicated to providing superior air filtration solutions tailored to meet the diverse needs of our clients. We take pride in our specialized Bag-in-Bag-Out (BIBO) filter housing and unit production, offering a range of customized options designed for optimal contamination control and efficiency. Our bespoke BIBO systems include four distinct configurations:
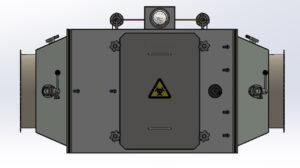
(assembled from a single HEPA)
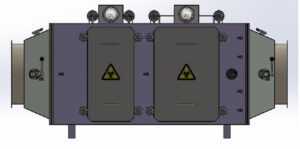
(assembled from medium and HEPA filters)
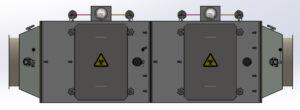
(assembled from two HEPA filters)
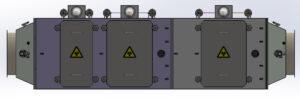
(assembled from two HEPA filters)
- Single High Efficiency: This unit is assembled using a single High-Efficiency Particulate Air (HEPA) filter, designed for environments requiring precision air filtration. It captures 99.97% of airborne particles, making it ideal for sensitive applications where clean air is paramount.
- Medium Efficiency + High Efficiency: Combining a medium-efficiency pre-filter with a HEPA filter, this BIBO housing is engineered to extend the lifespan of the HEPA filter by capturing larger particles beforehand, thus enhancing overall filtration effectiveness and operational efficiency.
- Double High Efficiency: Our double HEPA configuration is assembled with two consecutive HEPA filters. This setup provides an advanced level of air purification, significantly reducing the concentration of ultrafine contaminants, and is suited for the most demanding cleanroom conditions.
- Medium Efficiency + Double High Efficiency: By integrating a medium efficiency pre-filter with two HEPA filters, this model delivers heightened levels of air cleanliness. The initial layer captures larger particulates, allowing the dual HEPA filters to effectively remove finer particles, thereby providing robust protection against a wide spectrum of contaminants.
YOUTH's Material & Key Parameters
Stand module has three airflow options 1700m³/h, 3400m³/h, and 4250m³/h.
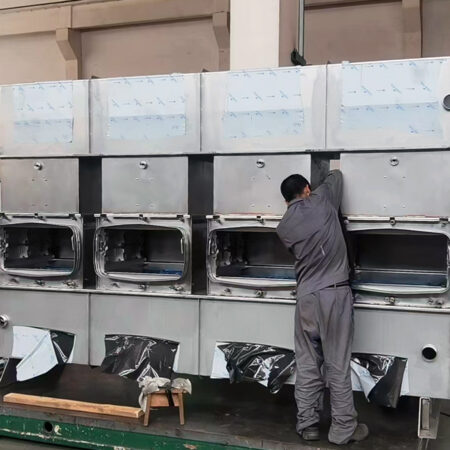
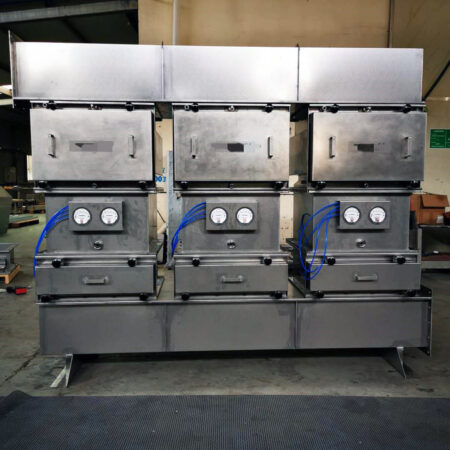
- Material Selection: Opt for premium 304 stainless steel or durable cold-rolled sheet metal to fabricate the equipment housing, providing robust durability and resistance to corrosion.
- Construction Standards: Use materials with a minimum thickness of 2.0mm to ensure structural integrity and longevity of the equipment.
- Welding Quality: Employ continuous welding techniques on all pressure-bearing joints and seams, eliminating any potential air gaps for airtight sealing.
- Pressure Tolerance: Construct the housing to endure pressure differentials of up to ±2500pa, thereby ensuring safe operation under various environmental stressors.
- Safety Assurance: Through meticulous construction and choice of high-grade materials, confirm that the equipment meets or exceeds industry safety standards for pressure resistance and air purity control.
Streamlined Linear Scanning Process:

- Whole-section Scanning Approach: The method encompasses scanning the entire cross-section of the filter’s air outlet in a single, comprehensive motion, connecting seamlessly with an external scanning port.
- Continuous Sampling Operation: Throughout the scanning procedure, the full sampling head remains active, ensuring consistent and thorough assessment.
- Efficient Design Simplicity: The system’s straightforward architecture allows for rapid scanning, significantly reducing the duration of the process.
- Market Prevalence: Due to its swift scanning capability and high efficiency, this linear scanning technique is favored and prevalent in commercial applications.
Sequential Row-by-Row Scanning Technique
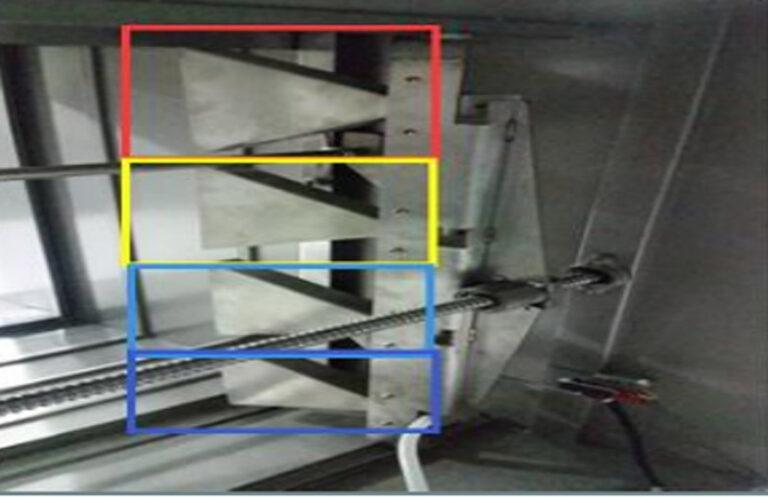
- Four-Head Sampling Strategy: This approach utilizes four distinct sampling heads, each aligning with one external scanning port to comprehensively assess the entire air outlet cross-section of the filter.
- Alternating Active Sampling: During the scanning process, activation occurs sequentially—only one sampling head operates at a given time, while the remaining three standby, ensuring focused analysis.
- Methodical Scanning Sequence: For instance, when the second sampling head is engaged, the first, third, and fourth heads remain inactive. This pattern continues, rotating through each sampling head to complete a full scan.
- Intricate and Extended Duration: Although the process is more complex and time-intensive compared to other methods, it delivers high precision in its scanning results.
Personnel Training Requirements
Comprehensive training protocols are essential for both operators and maintenance personnel:
Personnel Category | Training Focus | Training Duration |
---|---|---|
Operators | System monitoring, alarm response, documentation | 4-8 hours |
Maintenance Team | Filter change procedures, bag handling protocols | 8-16 hours |
Supervisory Staff | System overview, compliance requirements, risk assessment | 4-6 hours |
Validation Team | Testing methodologies, acceptance criteria, documentation | 8-12 hours |
EHS Personnel | Exposure risk assessment, waste handling protocols | 4-8 hours |
Training should include both theoretical components and hands-on practice, with particular emphasis on proper bag-out techniques to maintain containment integrity. Periodic refresher training is recommended, particularly for maintenance personnel who may perform filter changes infrequently.
Documentation and Validation Planning
The documentation package associated with BIBO implementation includes several critical components:
Installation qualification (IQ) protocols verifying proper system installation
Operational qualification (OQ) testing system functionality
Performance qualification (PQ) verifying containment efficacy
Standard operating procedures (SOPs) for routine operation
Maintenance procedures including detailed filter change protocols
Emergency response procedures for system failures
Training materials and competency assessment tools
Ongoing performance verification protocols
These documents should be developed in accordance with applicable regulatory requirements and organizational quality systems, with appropriate review and approval before implementation.
Regulatory Compliance Considerations
Implementation planning must address the specific regulatory framework governing the facility:
FDA regulatory requirements for pharmaceutical and healthcare applications
Nuclear Regulatory Commission (NRC) standards for radiological implementations
OSHA compliance for worker safety considerations
EPA requirements for environmental protection
Industry-specific standards such as USP <800> for hazardous drug handling
Many organizations benefit from conducting formal regulatory gap analyses during the planning phase, identifying specific compliance requirements that will impact implementation decisions.
The comprehensive nature of these implementation considerations underscores the importance of approaching BIBO system deployment as a cross-functional project rather than a simple equipment purchase. Organizations that invest in thorough planning typically experience smoother implementation processes, faster validation completion, and more reliable ongoing performance.
YOUTH BIBO Systems' Structural and Functional
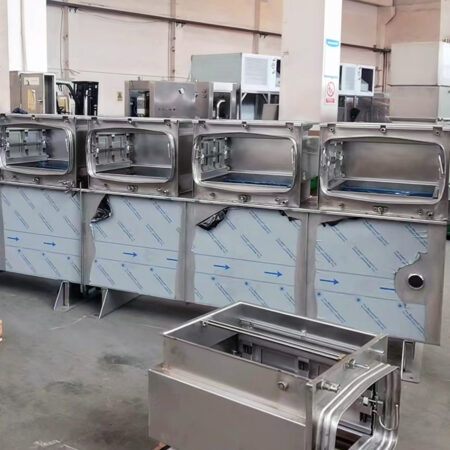
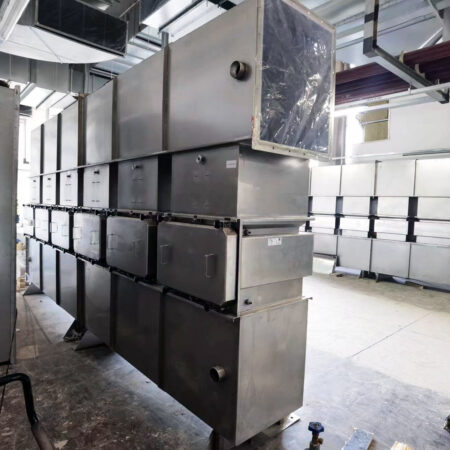
- Built to Withstand: The boxes are crafted by YOUTH to handle up to -2500Pa pressure for a duration of 60 minutes without any signs of damage or permanent alteration in form, in line with the demands of the exhaust device standard (JG/T497-2016).
- Guaranteed Sealing: Each BIBO system showcases exceptional sealing capabilities, maintaining air tightness at high pressures of both +3600Pa and -3600Pa, compliant with the technical specifications of exhaust devices and client-specific criteria for air permeability.
- Uniform Aerosol Levels: By generating dust upstream through reserved holes and employing a high-efficiency pre-filter, the aerosol concentration at nine strategically placed sampling points upstream deviates no more than ±20% from the average—ensuring uniformity that meets all pertinent standards.
- Precise Leak Discovery: Engineered for accuracy, the systems can detect and locate artificial leakages fashioned on reference filters with a standard gauge stainless steel needle, fulfilling all regulatory requirements for effective leak detection.
- Proven Disinfection Protocols: Disinfectants are injected into the system through designated ports, successfully passing biological safety tests including use of thermo-tolerant bacterial spores, ensuring comprehensive disinfection to meet official health and safety guidelines.
- Valves of Versatility: Available in sizes ranging from DN100 to DN800 with customizable square valves, these are constructed from SUS304 and equipped with TFE/silicone seals. They are available for manual, electric, or pneumatic operation, with a finish that may be drawn or sandblasted according to preference. Their performance remains within the permissible leakage rate even after extensive use.
- Durable Sealing Strips: Crafted from silicone capable of enduring extreme temperature fluctuations and resistant to chemical agents, these sealing strips come with the assurance of quality backed by CNAS and SGS certification.
- Adaptable Safety Bags: Standard at 2m in length but customizable to meet various operational needs, these bags are made from PVC/polymer materials and are resilient against extreme temperatures and chemical reactions, ensuring reliable performance.
Performance Metrics and Validation Protocols
The effectiveness of Bag In Bag Out (BIBO) systems is determined through rigorous performance validation using established metrics and standardized testing methodologies. These protocols not only verify proper system function but also generate the documentation necessary for regulatory compliance and quality assurance purposes.
Key Performance Indicators
BIBO system performance is assessed through several critical parameters:
Containment efficiency measured through aerosol challenge testing
Housing leak integrity verified via pressure decay testing
Airflow uniformity across the filter face
Pressure differential stability during normal operation
System integrity during simulated filter change procedures
Particulate penetration rates under standardized test conditions
Recovery time following bag-out operations
These parameters provide quantifiable metrics for system performance, establishing baseline data for ongoing monitoring and compliance verification.
Leak Testing Methodologies
Housing integrity testing represents a fundamental validation requirement, typically conducted using established protocols:
Pressure decay testing: Pressurizing the housing to a predetermined level (typically 1000 Pa) and measuring pressure loss over time (acceptance criterion typically <0.1% pressure loss per minute)
Soap bubble testing: Applying soapy water solution to potential leak points while the housing is under positive pressure
Halide leak detection: Using specialized detectors to identify minute leaks in pressurized systems
Aerosol challenge testing: Introducing upstream challenge aerosol and measuring downstream penetration
These tests are typically performed both during initial validation and as part of periodic requalification, with test methods selected based on facility requirements and applicable regulations.
Filter Performance Verification
The filtration efficiency of installed filters requires verification through standardized testing:
In-situ filter leak testing using PAO or DOP aerosol challenge
Scan testing of filter face and seals per IEST-RP-CC034
Upstream concentration uniformity verification
Upstream/downstream concentration ratio determination
Penetration calculation and comparison to acceptance criteria
These procedures verify not only the integrity of the filter media but also the effectiveness of the seal between the filter and housing, a critical factor in overall system performance.
Validation Documentation Requirements
A comprehensive validation package typically includes:
Validation master plan outlining the validation approach
Installation qualification (IQ) documenting proper installation
Operational qualification (OQ) verifying system functionality
Performance qualification (PQ) confirming containment effectiveness
Test reports with raw data and calculated results
Calibration certificates for test equipment
Personnel qualification records for testing technicians
Deviation reports and resolution documentation
Final validation summary with approval signatures
This documentation provides the evidence base for regulatory compliance and serves as a reference point for future system modifications or troubleshooting.
Ongoing Performance Monitoring
Beyond initial validation, continuing performance verification typically includes:
Monitoring Parameter | Frequency | Acceptance Criteria |
---|---|---|
Visual inspection | Weekly | No visible damage or leaks |
Pressure differential | Continuous | Within ±20% of setpoint |
Filter integrity test | Annual | 99.97% efficiency minimum |
Housing leak test | Biennial | <0.1% pressure loss per minute |
Operator technique verification | Annual | No procedural deviations |
Airflow verification | Quarterly | Within ±10% of specification |
These ongoing verification activities ensure that performance remains consistent throughout the system lifecycle, with any deterioration identified and addressed promptly.
Industry-Specific Validation Considerations
Validation protocols often incorporate industry-specific elements:
Pharmaceutical applications: Process simulation testing using surrogate materials to verify containment during realistic operating conditions
Nuclear implementations: Radiological monitoring during simulated filter changes
Semiconductor applications: Particle counting upstream and downstream during normal operation
Biological containment: Microbiological sampling following filter changes
These specialized protocols address the unique risks and regulatory requirements associated with different implementation contexts.
The validation of BIBO systems represents a significant investment in time and resources, but delivers crucial performance documentation that supports both operational confidence and regulatory compliance. Organizations implementing these systems should develop comprehensive validation strategies early in the planning process, ensuring that all necessary protocols and documentation requirements are identified and addressed systematically.
YOUTH's Innovative Airflow Configurations
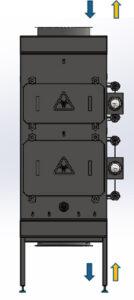
Cleanroom BIBO Unit with
Top-Down Airflow
- Vertical Airflow Design: The Cleanroom BIBO unit can be installed vertically, enabling airflow to move in either a top-down or a bottom-up direction.
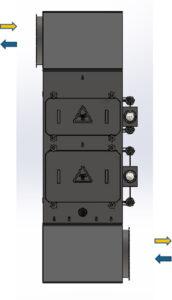
Cleanroom BIBO Unit with
Left-to-Right Airflow via Elbow Duct
- Vertical with Elbow Duct: When vertically installed, the BIBO unit includes an elbow duct which redirects the airflow to move horizontally, either from left to right or right to left.
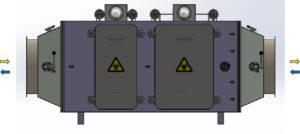
Cleanroom BIBO Unit with
Side-to-Side Airflow
- Horizontal Airflow Configuration: Designed for horizontal installation, the cleanroom BIBO unit facilitates airflow from left to right or right to left across the unit.
Streamlined Filter Section Definition
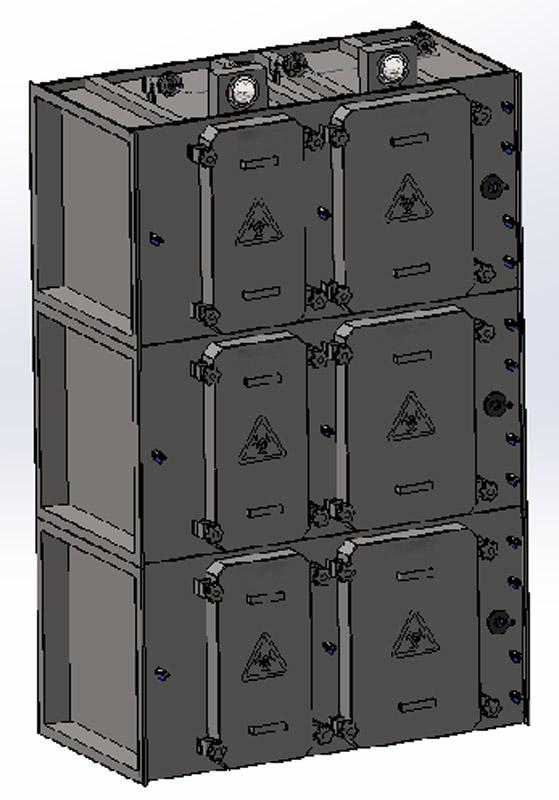
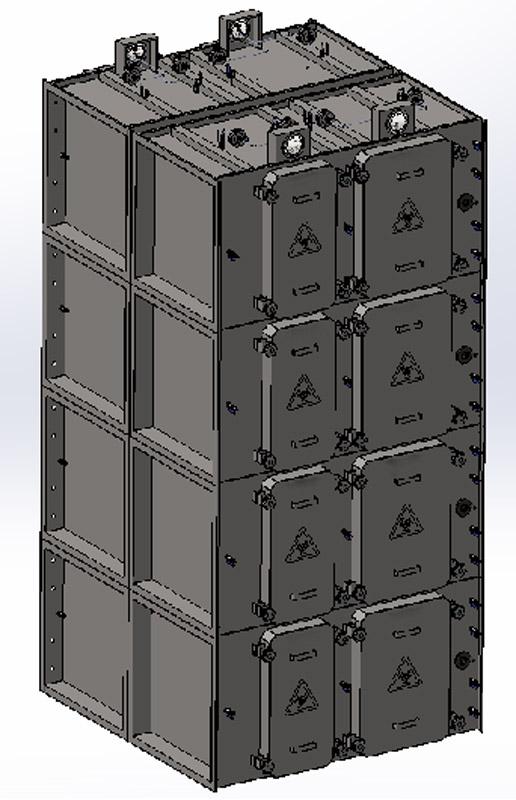
- Filter Unit Count: The term ‘filter section’ pertains to the tally of individual filter units that the airstream traverses when it passes in and out of the filter section, considering the inlet’s cross-sectional area (for example, configurations may include 1, 2, or 3 units).
- Assembly Capacity: A single filter section can accommodate an assembly of up to eight filter units, providing flexibility for various airflow requirements.
Applications Across Critical Industries
Bag In Bag Out (BIBO) systems have become essential infrastructure across multiple industries where containment of hazardous materials is paramount. The versatility of BIBO technology enables its implementation in diverse environments, each with unique operational parameters and regulatory frameworks.
Pharmaceutical Manufacturing Environments
Within pharmaceutical production facilities, BIBO systems play a critical role in maintaining product integrity and personnel safety. Specific applications include:
Active Pharmaceutical Ingredient (API) manufacturing suites where potent compounds require absolute containment
Formulation areas processing cytotoxic substances or highly potent compounds
Fill/finish operations requiring robust contamination control
Research and development laboratories handling novel compounds with unknown toxicity profiles
Quality control testing areas for potent product analysis
Pharmaceutical implementations typically require compliance with cGMP regulations, with BIBO systems providing documented evidence of containment efficacy. In facilities manufacturing highly potent compounds (OEL < 10 μg/m³), BIBO systems often serve as a critical engineering control within a comprehensive containment strategy.
Biotechnology Research and Production
The biotechnology sector presents unique containment challenges addressed effectively by BIBO implementations:
Biosafety Level 3 (BSL-3) research facilities handling infectious agents
Vaccine production suites with stringent cross-contamination prevention requirements
Cell and gene therapy manufacturing environments
Biocontainment facilities working with novel organisms
Animal research facilities managing allergens and pathogens
In these applications, BIBO systems typically interface with specialized HVAC systems designed for directional airflow and often incorporate additional features like ultraviolet germicidal irradiation (UVGI) or chemical decontamination capabilities.
Nuclear Facilities and Radiological Applications
The nuclear industry represents the historical origin of BIBO technology, with contemporary applications including:
Nuclear power plant filtration systems for radioactive particulates
Fuel processing facilities requiring absolute containment
Decommissioning operations where radioactive dust control is essential
Medical radioisotope production facilities
Research institutions handling radioactive materials
These implementations must comply with stringent nuclear regulatory requirements, including NQA-1 quality assurance protocols and specific testing methodologies like DOP penetration testing and pressure decay verification.
Healthcare Facility Infrastructure
BIBO systems have become increasingly common in healthcare settings:
Isolation rooms for patients with highly infectious diseases
Laboratory facilities handling dangerous pathogens
Autopsy suites processing high-risk cases
Pharmacies compounding hazardous drugs
Central sterile processing departments
In healthcare applications, BIBO systems often form part of a comprehensive infection control strategy, working in concert with other engineering controls to create safe working environments for healthcare professionals while protecting vulnerable patient populations.
Microelectronics and Semiconductor Manufacturing
The exacting requirements of semiconductor fabrication have driven specialized BIBO implementations:
Cleanroom environments requiring ultrafine particle control
Lithography areas with strict contamination protocols
Chemical processing sections handling aggressive compounds
Advanced packaging facilities requiring exceptional air quality
Research and development spaces for next-generation semiconductor technologies
In these applications, the focus shifts from personnel protection to product protection, with BIBO systems designed to maintain the pristine environments necessary for manufacturing components with nanometer-scale features.
Industrial Applications with Hazardous Materials
Beyond these specialized sectors, BIBO systems find application in various industrial settings:
Chemical manufacturing facilities processing toxic substances
Battery production facilities handling fine particulates
Nanotechnology research and production environments
Advanced materials laboratories working with novel compounds
Industrial processes generating carcinogenic byproducts
Each application domain presents unique challenges that influence BIBO system design, from chemical compatibility considerations in aggressive environments to exceptional cleanliness requirements in semiconductor applications. This adaptability across industrial contexts demonstrates the fundamental soundness of BIBO engineering principles and explains their growing adoption as best practice for containment across critical industries.
YOUTH BIBO Housing System's Specifications
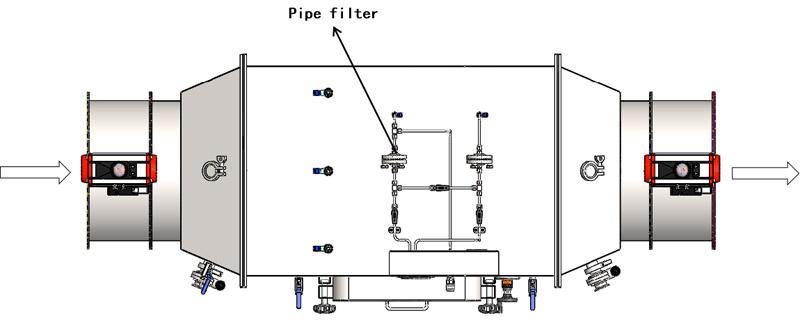
- High-Efficiency Filtration: Achieves a minimum of 99.97% particle capture rate for those sized at 0.3 micrometers.
- Rigorous Air Tightness: Maintains air leakage from the housing at less than 0.25% of its net volume per hour, even under pressures of ±3500Pa.
- Robust Pressure Tolerance: Designed to withstand a negative pressure of -2500Pa for an hour with no lasting structural changes, in compliance with exhaust device standards.
- Leak Detection Capabilities: Offers the option for either manual or automated leak detection scanning methods.
- Aerosol Concentration Consistency: Features nine strategically positioned measuring points near the upstream filter to ensure aerosol concentrations remain within ±20% of the mean.
- Sterilization and Filter Replacement: Employs an in-situ gas sterilization process followed by a secure and efficient bag-in-bag-out filter change procedure.
- Exceptional Corrosion Resistance: Constructed from 304 stainless steel, the housing is impervious to a wide range of chemical agents including disinfectants, cleaners, and various acidic and alkaline substances.
Implementation and Integration Considerations
Successful deployment of Bag In Bag Out (BIBO) systems requires careful planning and coordination across multiple organizational functions. The implementation process encompasses far more than simple equipment installation, involving comprehensive facility assessment, system integration planning, personnel training, and validation protocol development.
Site Preparation Requirements
Proper site preparation forms the foundation for effective BIBO implementation:
Structural assessment to verify adequate support for housing weight (typically 75-250kg per housing)
Spatial analysis ensuring sufficient clearance for safe bag-out operations (minimum 1m service area)
Utility evaluation including compressed air requirements for pneumatic systems
Electrical infrastructure assessment for monitoring and control systems
Verification of floor loading capacity (particularly for multi-filter array systems)
HVAC ducting evaluation to accommodate housing dimensions and airflow requirements
Organizations implementing BIBO systems should conduct thorough site surveys before finalizing system specifications, as retrofit implementations often present unexpected challenges requiring design adaptations.
System Integration Planning
BIBO systems must interface seamlessly with existing facility infrastructure:
HVAC system integration including ductwork transitions and airflow balancing
Building automation system (BAS) connectivity for monitoring and alarming
Fire safety system coordination including damper control integration
Electrical system connections for monitoring and control functionality
Facility monitoring system integration for performance tracking
IT infrastructure requirements for networked monitoring capabilities
The integration planning process should involve cross-functional stakeholders including facilities management, engineering, quality assurance, and EHS teams to ensure all operational requirements are addressed holistically.
Installation Process Considerations
The installation phase presents unique challenges requiring specialized expertise:
Housing placement requiring precise alignment with existing ductwork
Sealing system verification ensuring gastight connections
Pressure testing of the completed assembly before commissioning
Initial filter loading following validated procedures
Monitoring system calibration and verification
Startup testing and system balancing
Many organizations engage specialized contractors with BIBO-specific experience for installation, as improper installation can compromise system performance and invalidate subsequent validation efforts.
FAQs
How does a BIBO system work?
It works by enclosing the contaminated filter within a secured bag within the housing unit, which is then safely removed, preventing the escape of particulates.
What does the ‘bag-in-bag-out’ process involve?
The process involves placing the contaminated filter into a bag (and sometimes a second outer bag), sealing it, and removing it from the housing without releasing contaminants.
What is the typical pressure tolerance of a BIBO system?
BIBO systems are constructed to withstand various pressure differentials, often up to ±2500pa or higher, depending on design specifications.
Is leak detection part of a BIBO system’s functionality?
Yes, YOUTH’s BIBO systems include manual or automatic leak detection capabilities to ensure filter integrity.
Can BIBO systems be integrated with existing HVAC systems?
BIBO units can often be integrated with HVAC systems; however, compatibility and integration requirements should be verified with the manufacturer.
What considerations should be made when choosing a BIBO system?
Considerations include the type of contaminants, required level of containment, air-flow design, and integration with existing systems.
BIBO System Related Name
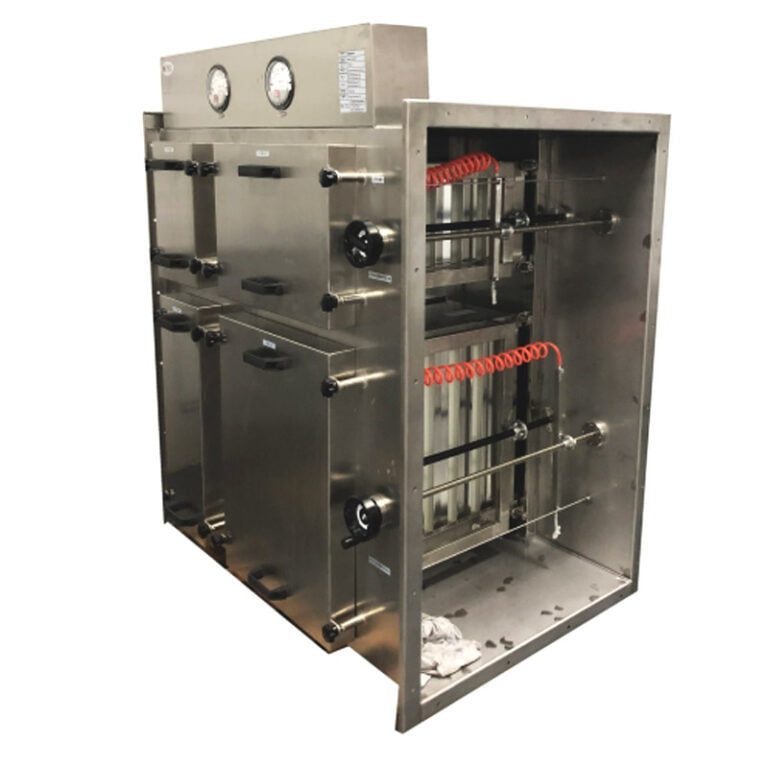
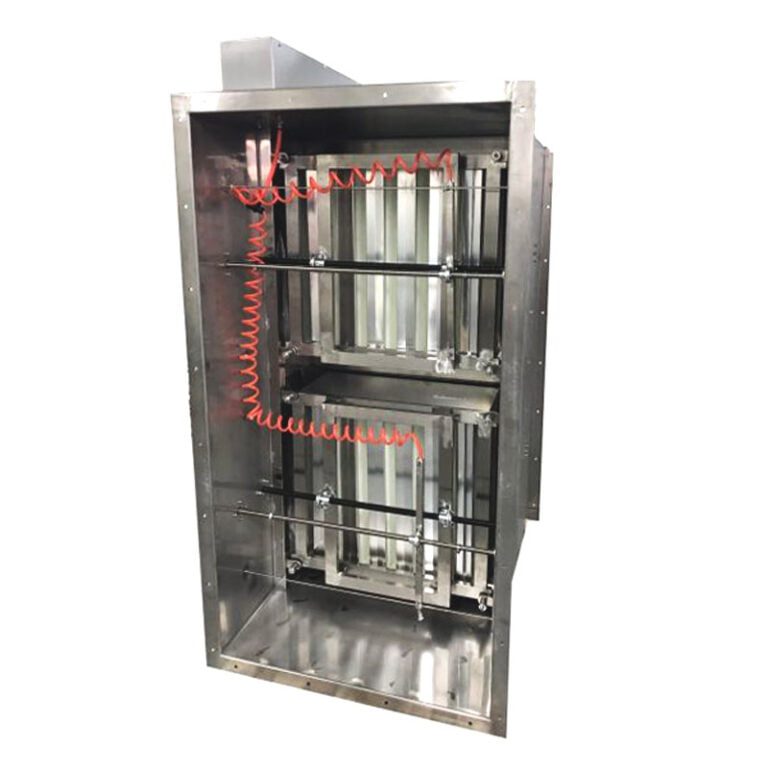
Bag-in-Bag-out HEPA System:
This refers to an entire air filtration system that includes HEPA filters and operates on the BIBO principle. It ensures that all the components needed to filter out airborne particles and biological contaminants comply with the BIBO safety measures. The entire process of replacing the HEPA filter is safely contained to prevent contamination.
Bag-in-Bag-out Filter Port
The “bag in bag out port,” in the context of a Bag-in-Bag-out (BIBO) system, is a feature that allows the connection of a bag (used for safely removing and disposing of contaminated filters) to the filter housing or unit. The port is an integral part of the BIBO system’s design to ensure airtight and safe handling of hazardous materials.
Bag-in-Bag-out Filter Housing
It is the protective casing that holds a filter—usually a HEPA filter—while providing a secure method to replace it without exposing the environment or personnel to dangerous contaminants. The housing is designed so that when the filter needs to be changed, it can be placed into a bag while still within the housing. Once sealed, it can be safely removed, thereby minimizing the risk of exposure.
Bag-in-Bag-out HEPA Filter
The HEPA filter is used within a BIBO system. HEPA filters are high-efficiency particulate air filters that trap a high percentage of dust, pathogens, and contaminants. When it’s time to change out a HEPA filter in a sensitive environment, the BIBO technique is used. The used filter is enclosed in a bag before it is removed from its housing, and a new filter is placed without releasing contaminants into the air.
Bag-in-Bag-out Bag
The “bag” in the Bag-in-Bag-out (BIBO) process refers to the specialized containment bags used in the replacement procedure of filters in BIBO systems. These bags are made of durable materials designed to seal off and contain the hazardous particles collected by the filter. During a filter change, the contaminated filter is placed directly into this bag while still within the filter housing, thus minimizing the risk of exposure to dangerous materials.
Bag-in-Bag-out Unit
The term “unit” in the context of a BIBO system typically refers to the entire filtration unit, which includes the filter housing, the HEPA filters, and any other components necessary for the unit to function correctly in a contamination-controlled environment. The BIBO unit will have mechanisms in place to allow for the safe replacement of filters, ensuring that operators and the environment are not exposed to the contaminants trapped in the filters. The entire unit is engineered to provide high-efficiency particulate air filtration while also allowing for safe maintenance practices through the BIBO procedure.
Related Contents:
- HEPA Housing Boxes in Pharmaceutical Manufacturing: Uses
- Bag-In/Bag-Out (BIBO) Systems: Operation and Maintenance Guide
- Emerging Trends in HEPA Housing Box Technology for 2025
- Hospital HVAC Systems: HEPA Housing Box Implementation Guide
- What is the Efficiency Rating of HEPA Housing Boxes?
- BIBO System Validation: Regulatory Requirements
- Aerospace HEPA Housing Box Requirements & NASA Standards
- Top 5 BIBO Containment Solutions for 2025
- Boosting Productivity with Advanced HEPA Housing Systems