What is the fan filter unit?
The fan filter unit is a device used to purify the air in a space. Generally installed on the ceiling, laminar airflow is maintained in a specific direction to maintain efficient removal of harmful particles in the air.
Mostly used in medical, pharmaceutical, electronics and other fields.
- Air Intake: The FFU draws in air from the cleanroom or from outside air.
- Pre-Filtering: The pre-filter captures larger particles to protect and extend the life of the main HEPA/ULPA filter.
- Main Filtration: The air then passes through a HEPA or ULPA filter, which captures very fine particles and microorganisms, providing a high level of air purity.
- Air Distribution: Finally, the clean, filtered air is distributed evenly back into the cleanroom.
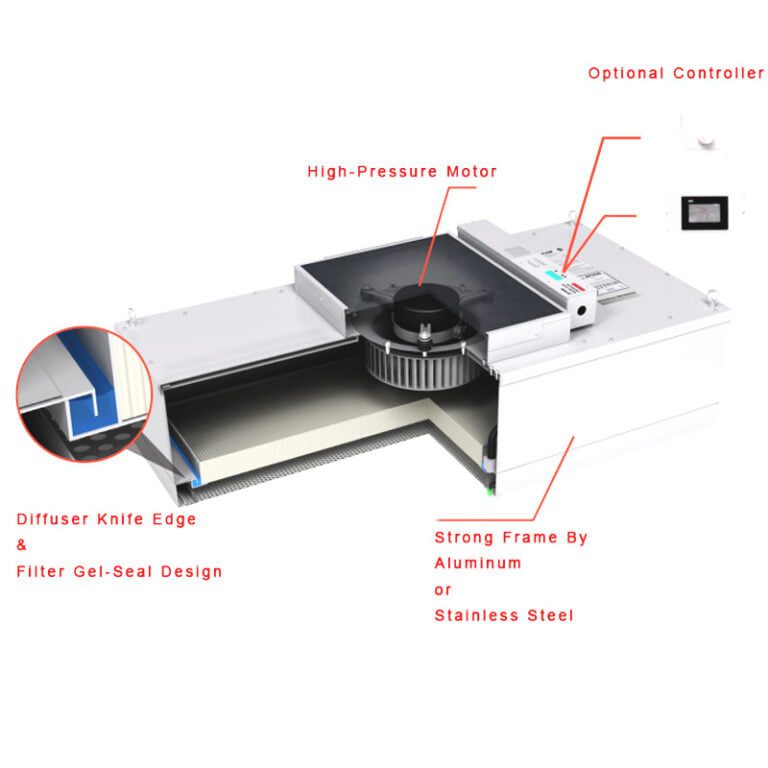
YOUTH's Advancing Fan/Motor Technology
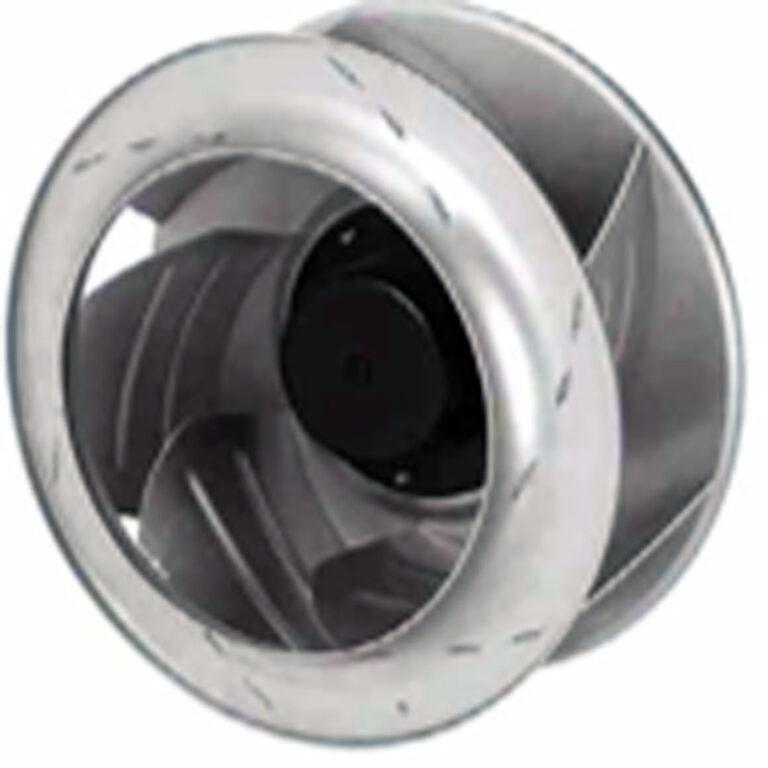
Implement cutting-edge, internationally recognized fan/motor technology that combines superior quality, energy efficiency, and whisper-quiet operation.
- Utilize high-efficiency outer rotor or inner rotor direct drive motors.
- Choose between AC or DC brushless motors.
- Optimize the centrifugal impeller design for high efficiency and ensure dynamic balance up to the ISO1940, G2.5 standard.
Optimizing FFU Air-flow of Fan
Advanced FFU internal airflow guiding structure design to enhance efficiency and reduce noise.
YOUTH High-Quality Air Filter Manufacturing
YOUTH’s Fan Filter Unit Manufacturer based in Wuxi, Jiangsu. utilize high-efficiency, low-resistance filter materials from reputable international brands, such as glass fiber and PTFE.
- Ensure the filters are manufactured using imported origami machines in a controlled environment of constant temperature and humidity.
- Conduct 100% leak detection and MPPS sampling inspection before the filters leave the factory.
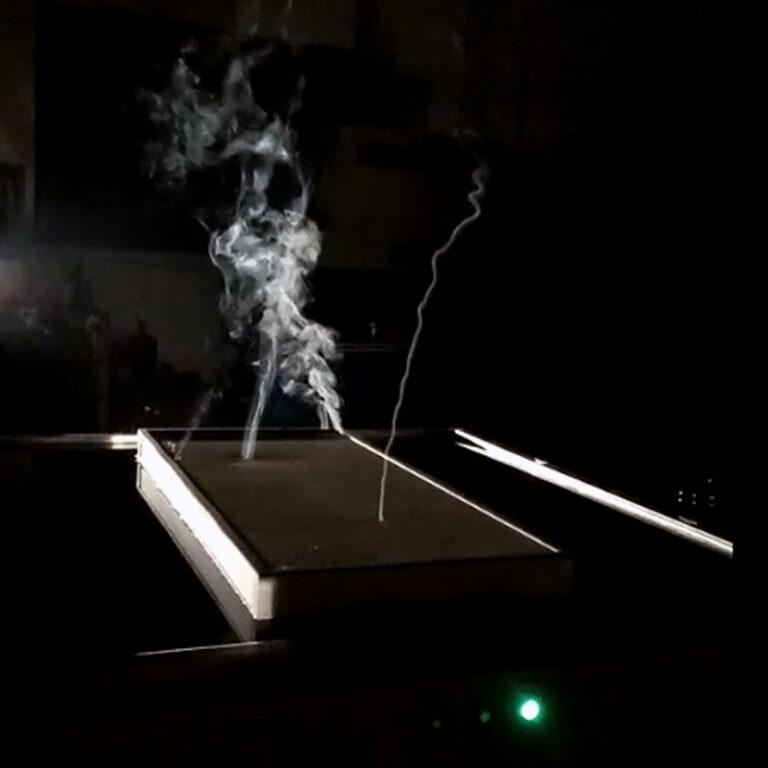
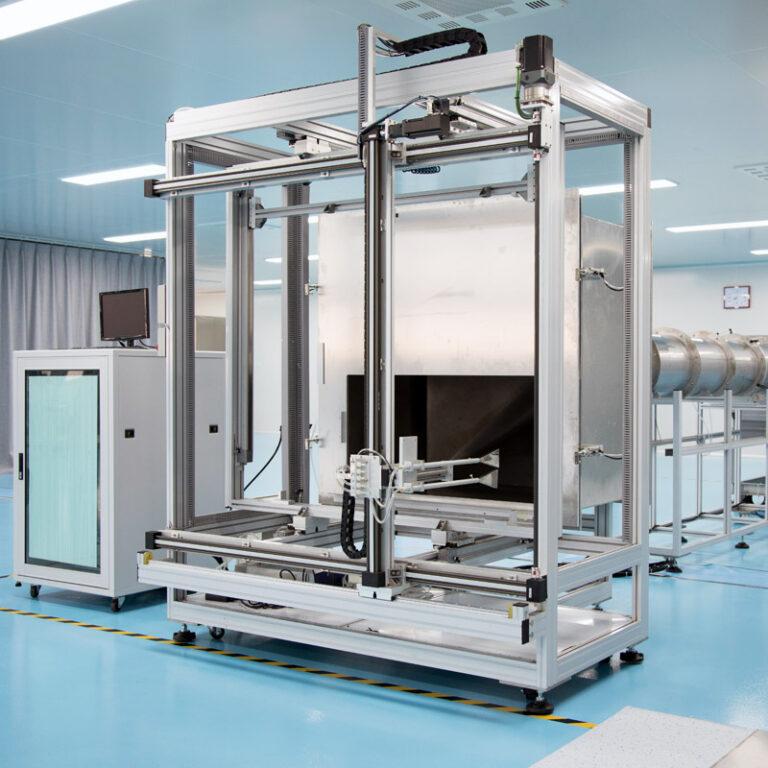
YOUTH Intelligent FFU Control
The intelligent FFU control system is designed to achieve both individual and group monitoring of FFU units. It provides suitable control methods and monitoring systems for various requirements, ranging from small-scale specific needs to large-scale integrated systems, such as IFAN1, IFAN5, IFAN7, etc.
YOUTH's Expert R&D in FFU Customized
YOUTH boasts a seasoned research and design team within the industry, offering tailored solutions to meet specific customer requirements.
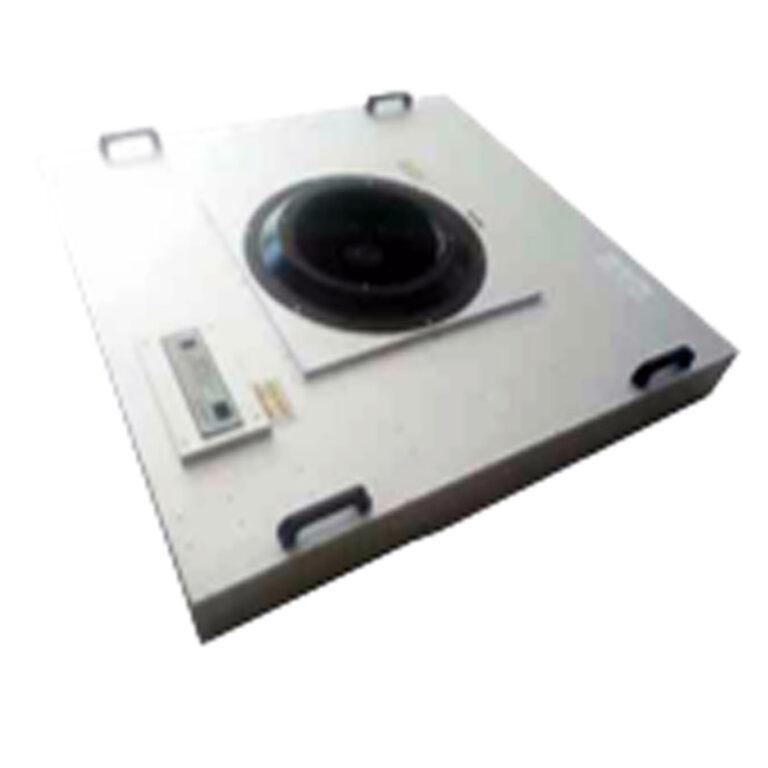
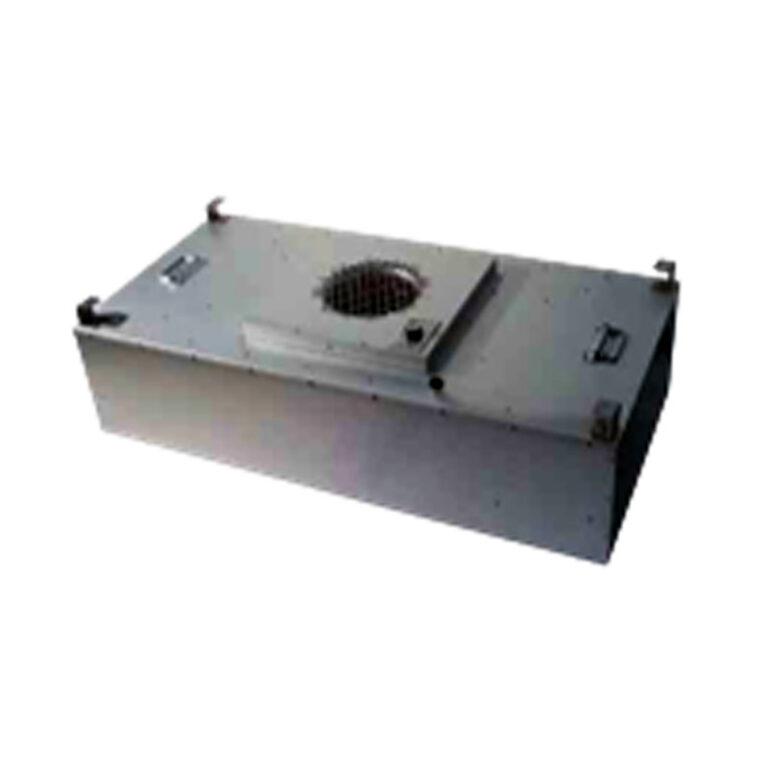
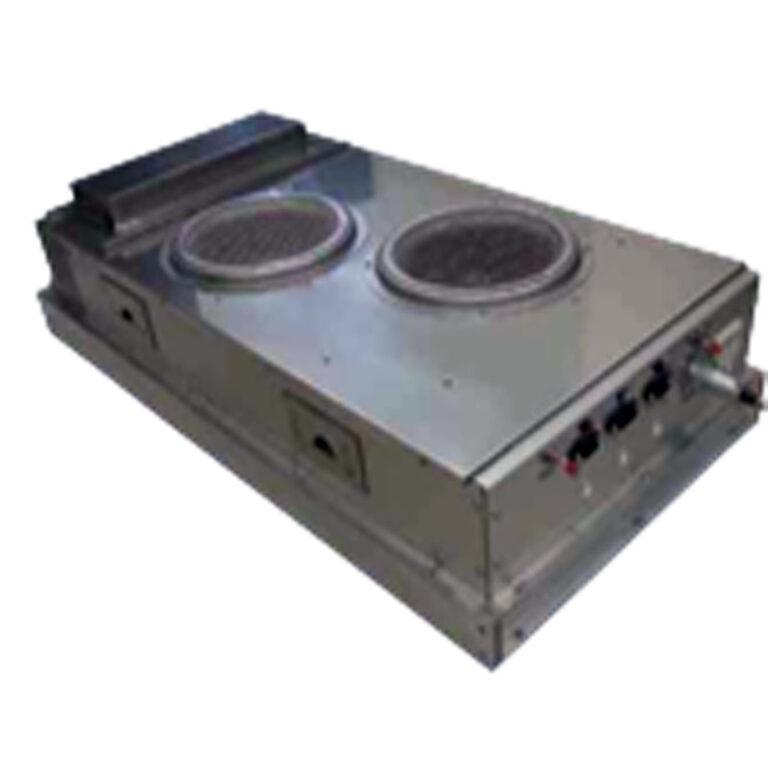
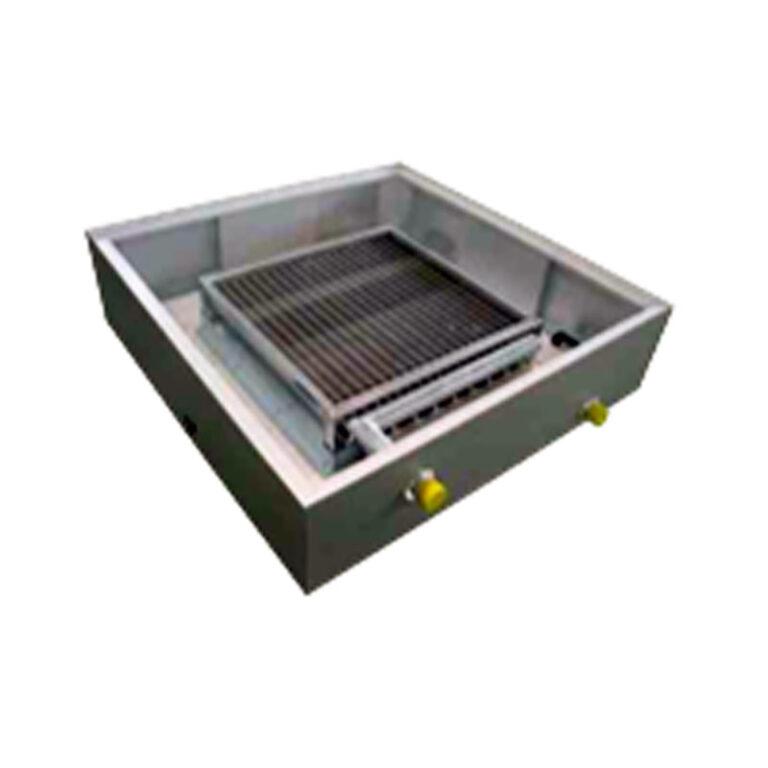
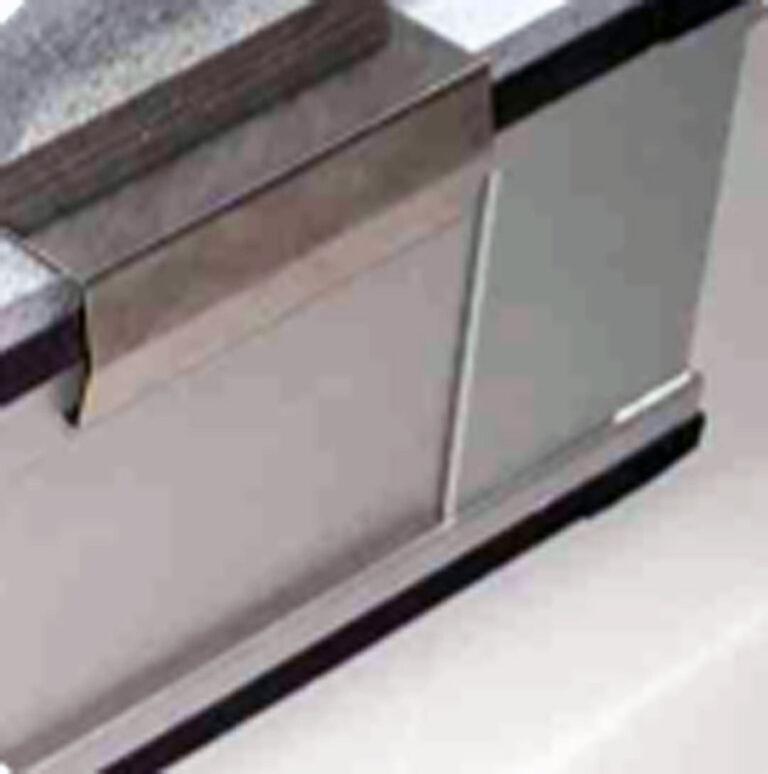
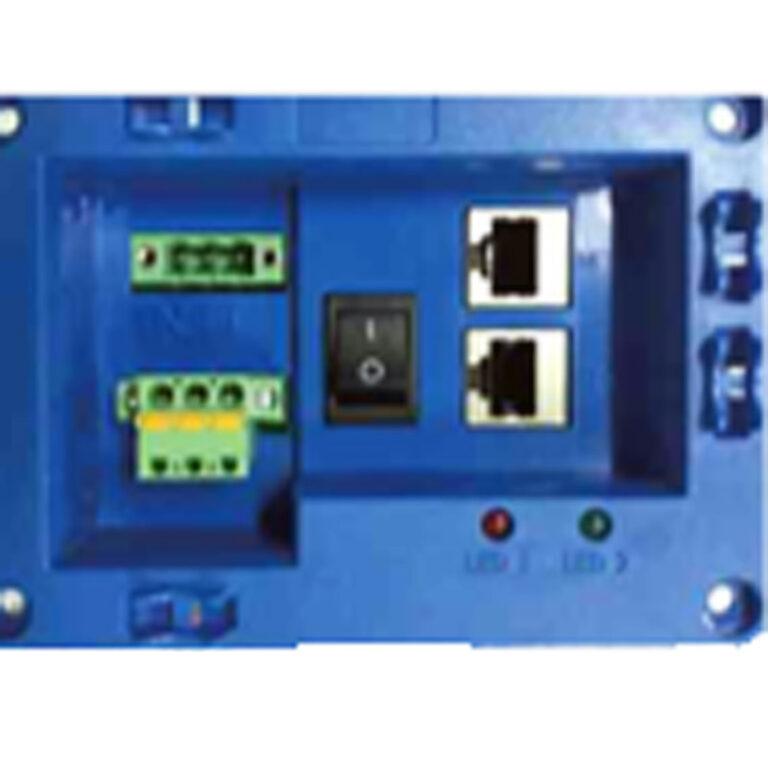
Custom Chemical Filtration for FFU
YOUTH offers bespoke chemical filtration solutions, designed to cater to unique customer needs, considering the specific processes, substances, and levels of chemical pollutants involved. We ensure a seamless blend of cleanliness and gas pollution management, efficiently removing acid gases such as SOx, NOx, HF, HCl, and acetic acid; alkaline gases including NH3 and amines; VOCs like siloxane, toluene, DOP, and PGMEA; as well as dopants like phosphorus and boron.
YOUTH's FFU Performance Parameters
Test conditions: air velocity = 0.45m/s, HEPA filter thickness = 70mm, ESP = 100Pa;
The height of the air inlet circle of 25mm~35mm should be added to the thickness of the above box.
Standard FFU’s types: 2×4, 2×2, 4×4 and more…
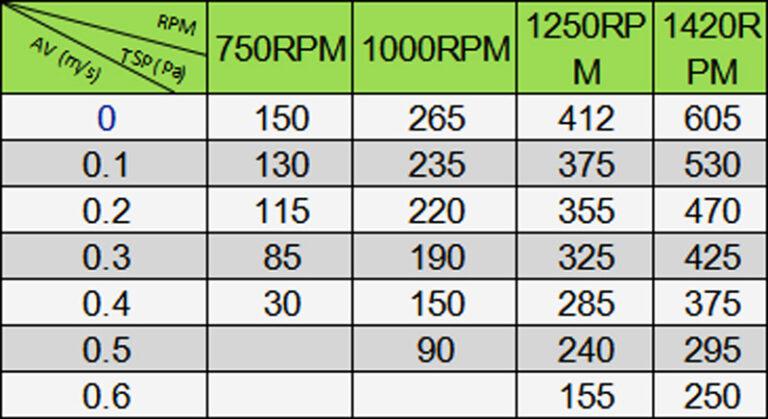
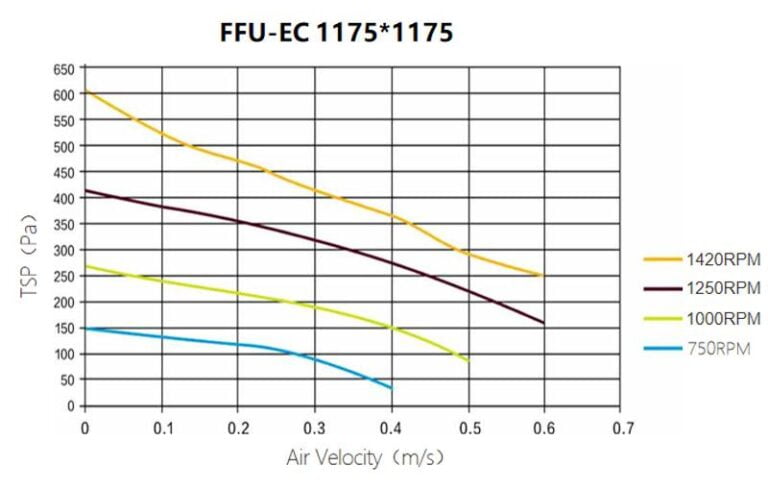
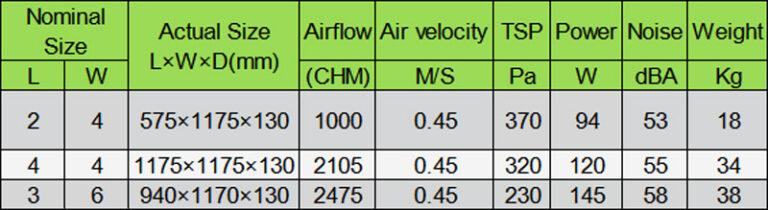
Control System Diagram of iFan 1 AC FFU
- Stable RS-485 Control: Reliable via intelligent modules and retransmission.
- Real-time Quality Check: Monitors communication for maintenance.
- Cloud Access: Ethernet and cloud-based monitoring.
- Multi-screen Support: Works with diverse displays and can be customized.
- Open Modbus Communication: Two-layer/single-layer formats.
- Graphical Interface: Easy symbol-based control.
Control system diagram of iFan 5 DC FFU
- Flexible control: Easily scales to thousands of FFUs with centralized management.
- Real-time monitoring: Tracks FFU status and alerts for quick issue resolution.
- Clear visualization: Color-coded maps help locate issues swiftly.
- Quick diagnostics: Pinpoints faults with specific codes, minimizing downtime.
- Persistent settings: Saved in memory, unaffected by power loss.
- Efficient maintenance: Identifies and resolves faults promptly.
- Multi-brand support: Manages both EBM and Fuji Electric motors simultaneously.
Control system diagram of iFan 7 DC FFU
- Scalable Control: Effortlessly scale by linking servers and hubs, as demonstrated by real-world cases with up to 45000 FFUs.
- Visual Status: Quickly identify issues by integrating layout and colors for FFU statuses.
- Flexible Speeds: Adjust FFU speeds with settings saved for seamless operation.
- Centralized Management: Centralize control through expandable hubs.
- Instant Monitoring: Monitor operations and promptly address issues with alarms.
FAQs
Can FFUs be customized to suit different cleanroom requirements?
Yes, Fan Filter Units (FFUs) can be tailored to fit specific cleanroom needs. This customization can include the type of filters used (HEPA or ULPA), motor types for efficiency, and additional features like UV-C sterilization for enhanced disinfection. YOUTH offers various FFU models to cater to different requirements, such as energy efficiency, high airflow, and advanced control options. Options like room-side replaceable components and integrated LED lighting are also available to match unique operational needs.
How do HEPA and ULPA filters in FFUs differ?
HEPA and ULPA filters have different filtration efficiencies. ULPA filters are more efficient than HEPA filters at trapping smaller particles, hence they are used in environments that require an even higher level of air cleanliness.
What are the standard sizes of FFUs?
Standard FFU sizes are typically designed to fit into a 2×4 or 2×2 feet grid in the cleanroom ceiling, but sizes can vary based on manufacturer offerings and specific cleanroom requirements.
How often do the filters in an FFU need to be replaced?
Filter lifespan can vary based on the cleanroom’s operational conditions, but it’s generally recommended to replace HEPA/ULPA filters every 3 to 5 years. However, some filters may last longer with proper pre-filtration and maintenance.
What is the typical noise level of an FFU?
The noise level of an FFU can range from 45 to 65 decibels (dB), depending on the fan speed and model. Modern FFUs are designed to be as quiet as possible to not disrupt the cleanroom environment.
How are FFUs installed in a cleanroom environment?
FFUs are typically installed into a T-bar grid system on the cleanroom ceiling. They can be hard-mounted or placed into the grid, and they usually require an external power source to operate.
Are there any specific maintenance procedures for FFUs ?
Regular maintenance procedures include inspecting and changing pre-filters, checking airflow, testing the integrity of HEPA/ULPA filters, and ensuring the motor operates correctly. It’s also essential to monitor the unit for excessive noise or vibration, which may indicate potential issues.
Related Contents:
- Bag-In/Bag-Out (BIBO) Systems: Operation and Maintenance Guide
- Mastering Clean Room Technology with Fan Filter Units (FFUs)
- How to choose FFUs and AHUs?
- Understanding the Mechanics of Fan Filter Units: A Detailed Guide
- Selecting the Right Fan Filter Unit for Your Cleanroom Needs
- Fan Filter Units: Balancing Efficiency and Cost-Effectiveness
- Fan Filter Units: Key to Quality Control in Cleanroom Manufacturing Processes
- Fan Filter Units: A Comprehensive Solution for Cleanroom Air Purification
- Innovative Fan Filter Units for the Next Generation of Cleanrooms