The Different Applications of: Dispensing Booth, Weighing Booth, and Sampling Booth
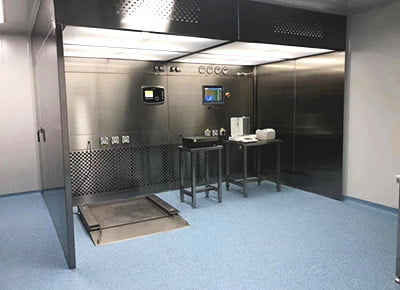
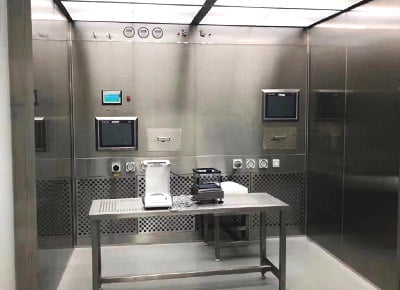
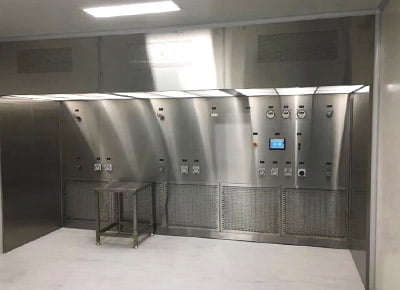
YOUTH’s Cleanroom Equipment offers a versatile range of specialized solutions to meet various industry needs. While Dispensing Booths, Weighing Booths, and Sampling Booths serve distinct purposes, they share common attributes while addressing unique requirements.
Common Attributes:
- Contamination Protection:
All three booths provide a controlled environment that shields against external contamination, ensuring accurate and precise operations. - Operator Safety:
Each booth offers a secure workspace, safeguarding operators from hazardous substances and promoting a secure working environment. - Regulatory Alignment:
Adherence to industry standards, such as ISO 14644 and FDA guidelines, is a common trait, reflecting YOUTH’s commitment to quality and compliance. - Customization:
All booths can be tailored to specific industry needs, adapting seamlessly to diverse requirements. - Workflow Efficiency:
Streamlined processes and reduced waste elevate operational efficiency across Dispensing, Weighing, and Sampling Booths.
Unique Attributes:
- Dispensing Booth:
– Crafted to manage sensitive substances within the realms of the pharmaceutical, biotechnology, and electronics sectors.
– Preserves the integrity of products and greatly reduces contamination risks throughout the dispensing activity.
– Prioritizes the eradication of contamination, meticulous handling of materials, and the safeguarding of personnel. - Weighing Booth:
– Unique negative pressure design ensures powders remain contained, preventing spread beyond the booth and protecting the internal cleanroom atmosphere.
– The powder weighing booth is dedicated to delivering precise and efficient measurements crucial for industries requiring high accuracy.
– Achieves consistent and accurate weight determinations by mitigating external airflow disruptions.
– Highlights economic and temporal gains by diminishing the need for corrections and waste, thereby enhancing operational productivity. - Sampling Booth:
– Tailored for sectors that depend on precise sampling to guarantee credible outcomes.
– Maintains a positive pressure zone to bar contaminants from entering and affecting the genuineness of samples.
– Outfitted with automated illumination to ensure clear visibility during sample collection activities.
In summary, YOUTH’s Cleanroom Equipment offers Dispensing, Weighing, and Sampling Booths that share core attributes of contamination protection, operator safety, regulatory alignment, customization, and workflow efficiency. These booths serve distinct purposes, catering to the specific needs of industries while upholding YOUTH’s commitment to excellence, innovation, and operational precision.
YOUTH Product's Features
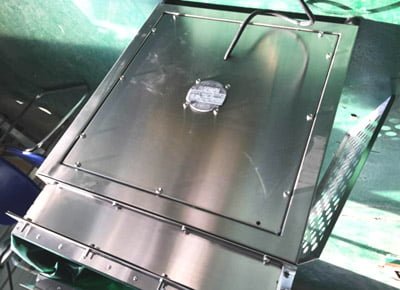
BLOWER
- Rosenberg Blower in the independent air box.
- Efficient and lubrication-free centrifugal blower.
- Built-in security measures for system and user protection.
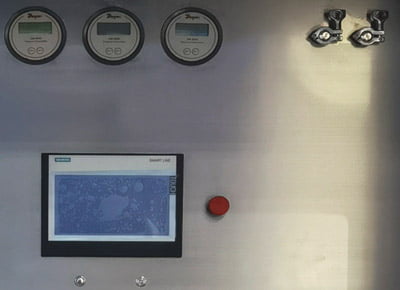
HEPA SUPPERVISED DEVICE
- HEPA located in the positive pressure section after the blower.
- Easy individual installation and removal for maintenance.
- Designed for convenient leak testing.
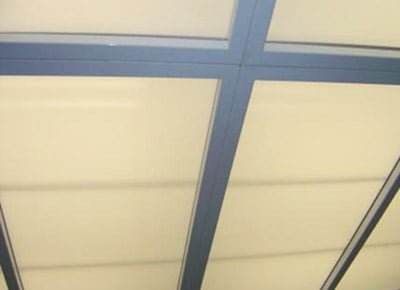
DIFFUSER
- 20mm SS304/SS316L protective frame
- Seamless integration with the booth’s outlet surface
- Designed for straightforward maintenance
- Improves air outlet consistency, illumination, and ventilation
- Option: Customizable with stainless steel full-perforation plates
- Option: Comes with recessed, flat tube lighting for ease of future maintenance
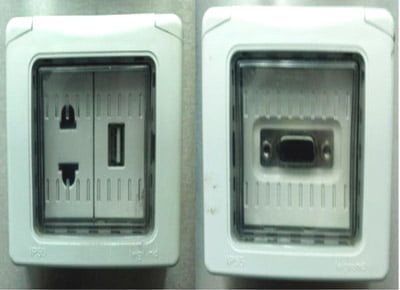
SOCKET
This socket is Mennekes/Philips type, modular for flexibility, accommodates 220V and 380V, and achieves IP55/IP65 sealing level for effective sealing performance.
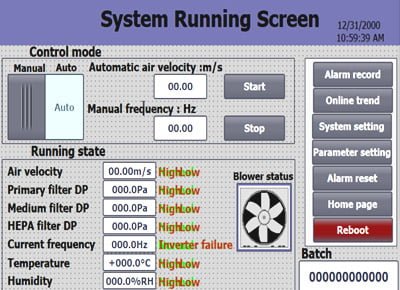
PLC CONTROL SYSTEM
SIEMENS PLC & HMI Adopt expandable CPU224 module (including storage system) Adopt SIEMENS (EM231, EM235 module) All electrical components use SCHNEIDER.
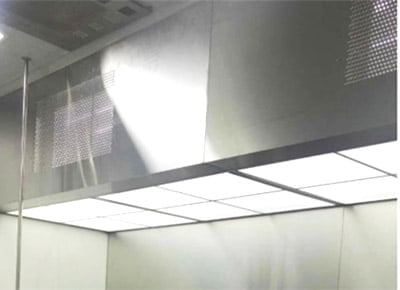
ILLUMINATION
Equipped with T5-bracket lamps with covers for efficient lighting at a min 350 Lux illumination. Using PET ceiling diffuser ensuring even and consistent illumination.
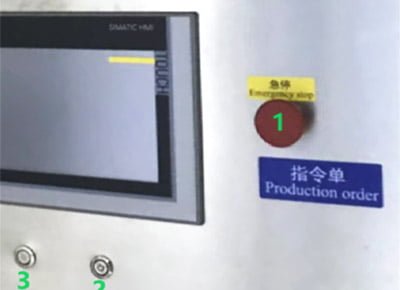
BUTTONS AND ALARM SYSTEM
Emergency Stop Button
POWER Switch
Audible Alarms

3-4 Access Authority
Level 1 Operator
Level 2 Engineer
Leavl 3 Administrator
Level 4 System
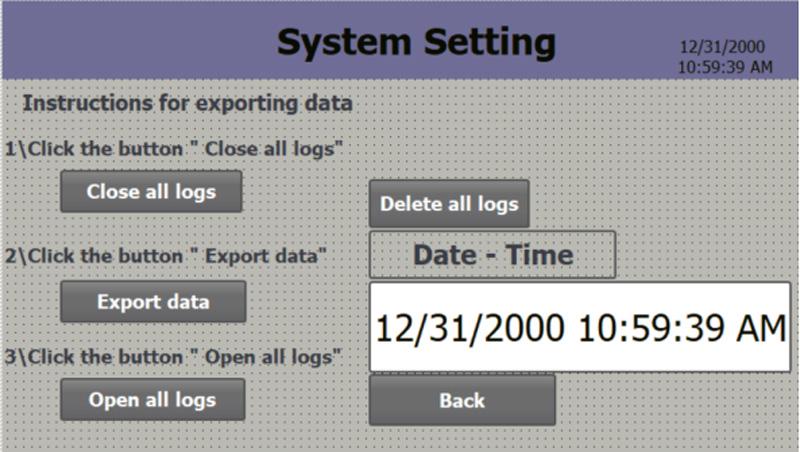
AUDIT TRIAL
We utilize Siemens encryption keys that conform to CFR21 requirements, ensuring that the dispensing process is traceable, verifiable, and compliant with all relevant regulations.
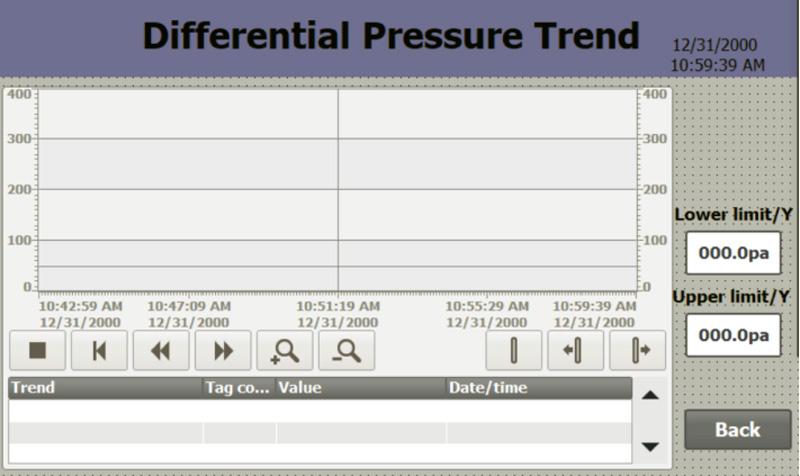
monitoring differential pressure trend
Monitoring differential pressure trend ensuring the safety and efficacy of pharmaceutical products while complying with regulatory requirements.

Monitoring temperature and humidity trend
Monitoring temperature, humidity in dispensing booths is critical. This helps to ensure that pharmaceutical products are manufactured and stored under the appropriate conditions
YOUTH's Weighing Booth VS. Others
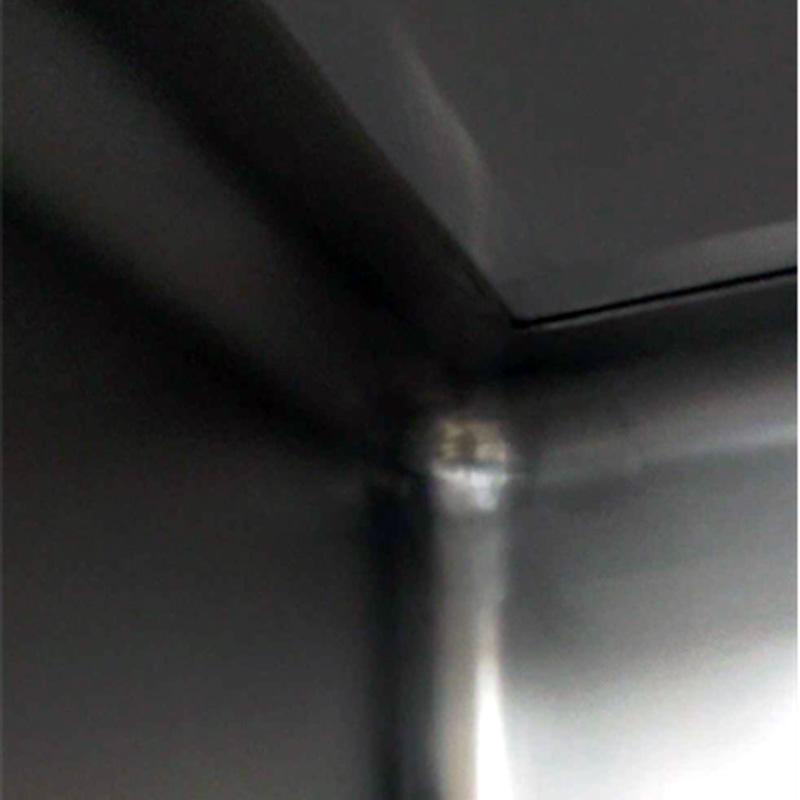
Youth's Structure
The Youth products feature an integrated structure with a circular arc design that prevents detachment and eliminates any welding gaps. This results in a visually appealing and graceful appearance.
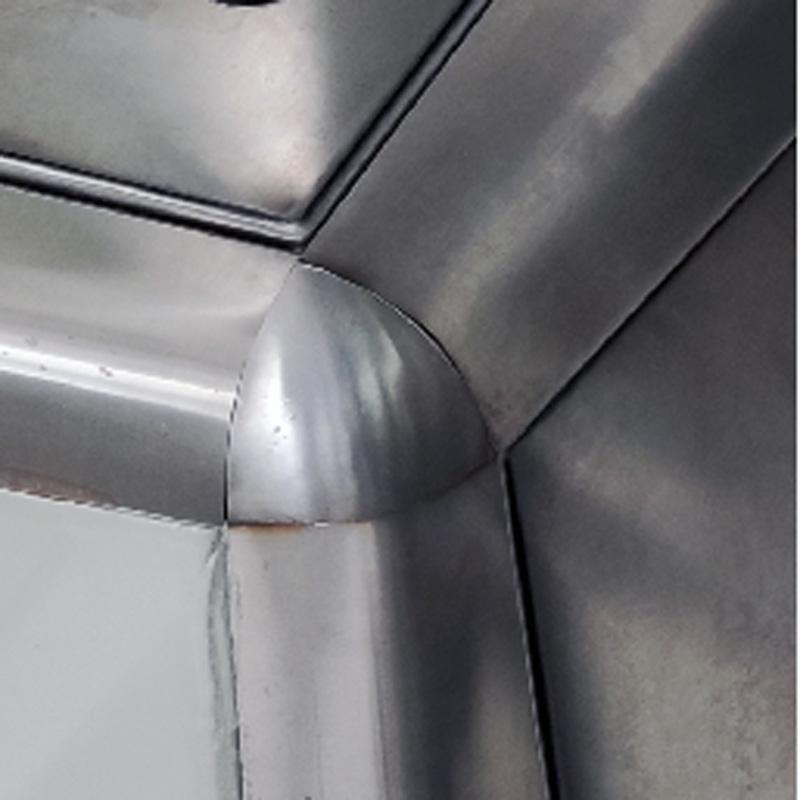
Other's Structure
Other manufacturers' products are either joined at right angles and bonded together, or attached with circular arc-shaped aluminum sheets that may detach over time, posing potential configuration hazards.
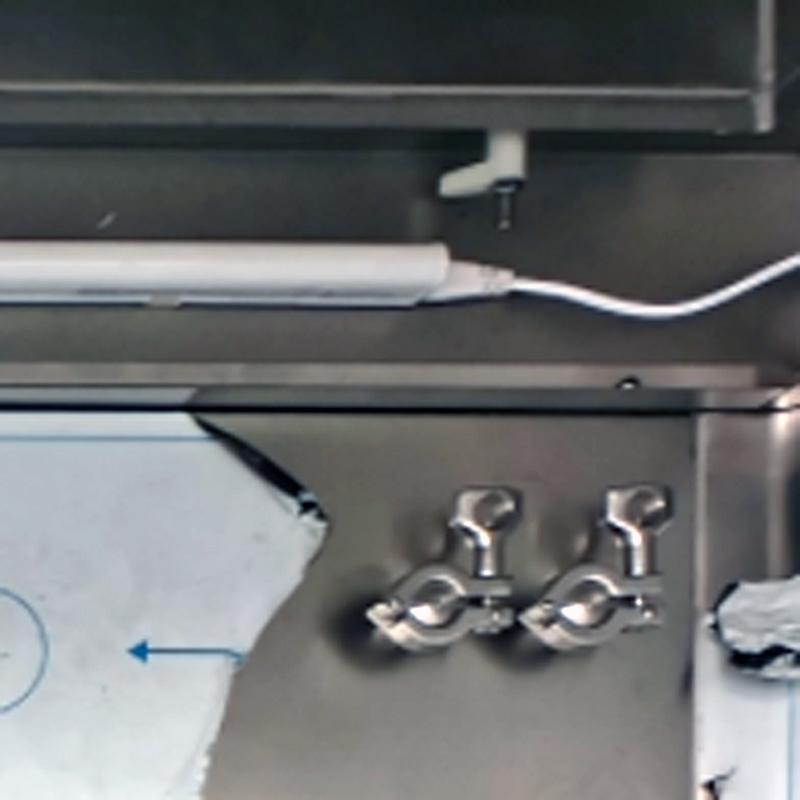
Youth's Bending
Youth products undergo full board bending and complete welding to minimize any gaps in the equipment. The filter's sealing knife edge is a crucial component that must guarantee zero leakage.
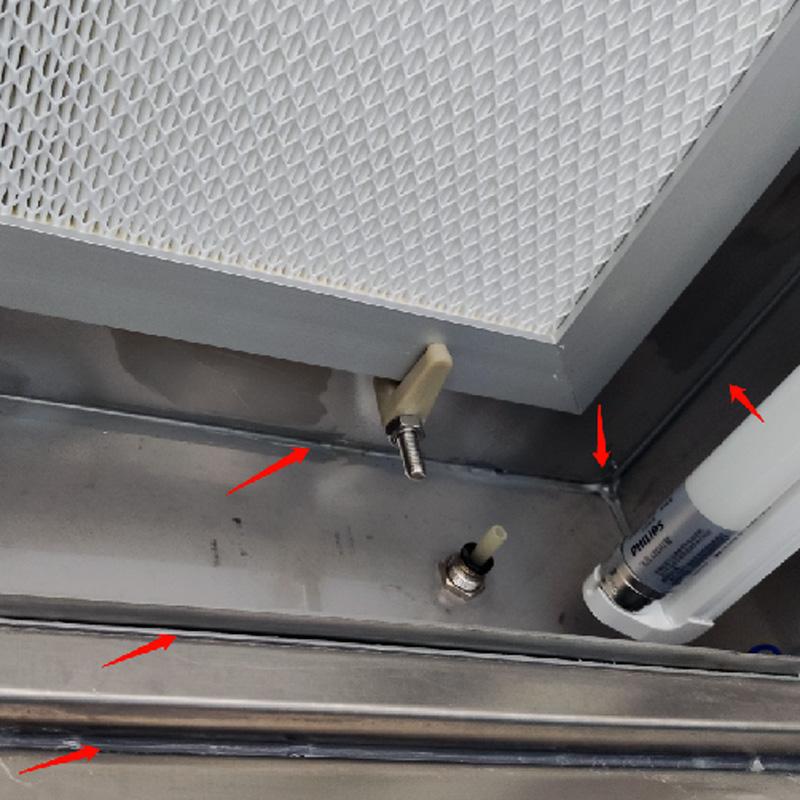
Other's Bending
Other manufacturers utilize spot welding and adhesive to seal their internal components, relying solely on glue to create a seal. This approach poses a significant risk of leakage over an extended period.
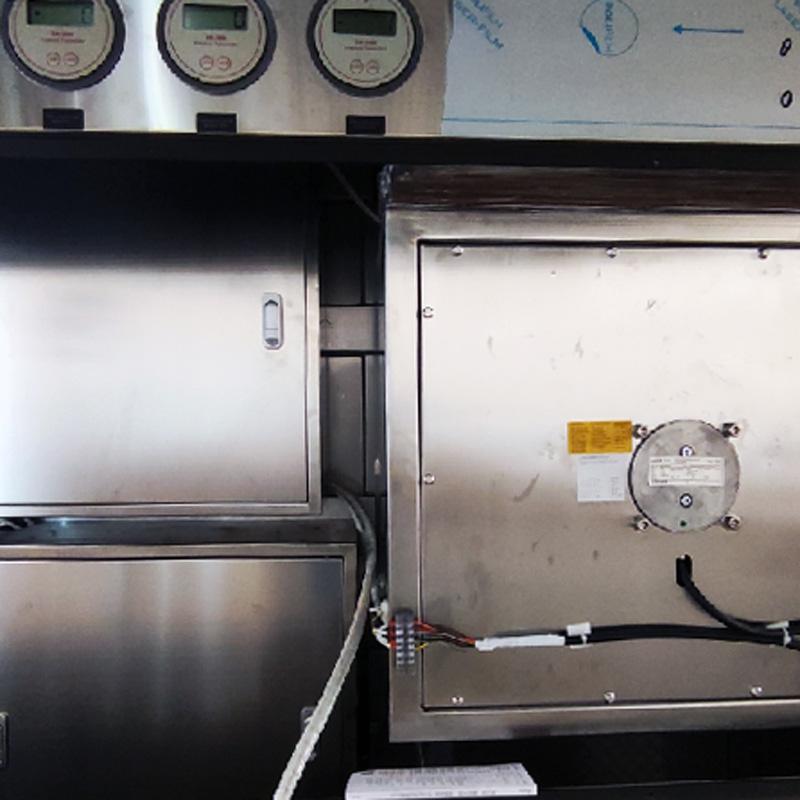
Youth's Box Design
Youth's invisible box boasts a tidy and well-maintained interior. Equipped with Rosenburg aluminum impellers, the fan is enclosed in a stainless steel box, effectively preventing the accumulation of dust. In contrast, other products' weighing chambers are prone to dust buildup over time, but our internal structure is designed for easy cleaning, ensuring hassle-free maintenance.
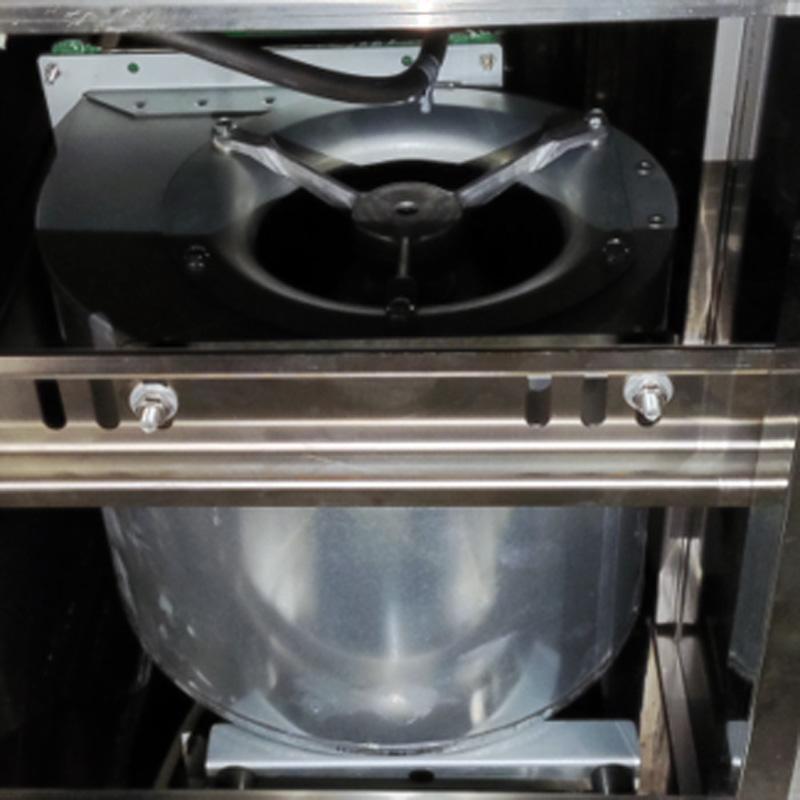
Other's BOX DESIGN
Other manufacturers' fans lack brand identification, are only galvanized, prone to rust, and lack a casing, with rough processing technology. The wiring is disorganized and poses a significant safety hazard due to exposed wiring ends, leading to electrical leakage. In contrast, Youth's products feature a superior fan design and organized wiring, ensuring a safe and reliable operation.
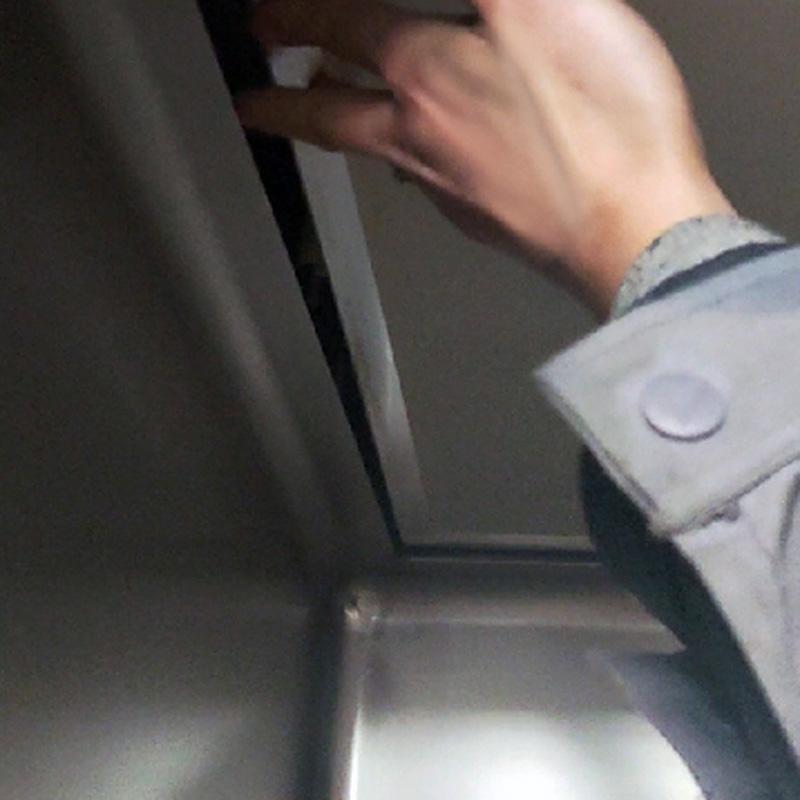
Youth's Maintenance
Youth's flow equalizing membrane design eliminates any exposed pressure blocks, making it effortless to maintain on a day-to-day basis.

Other's Maintenance
Other manufacturers' use of exposed briquettes makes daily cleaning an inconvenient task.

Youth's Magnetic Design
Youth's replacement filter features an innovative magnetic suction structure that eliminates pressure blocks and screws on the surface, ensuring a hassle-free replacement process. The punching method offers either a round or rectangular waist hole, making it easy to pull out the magnetic panel with fingers.
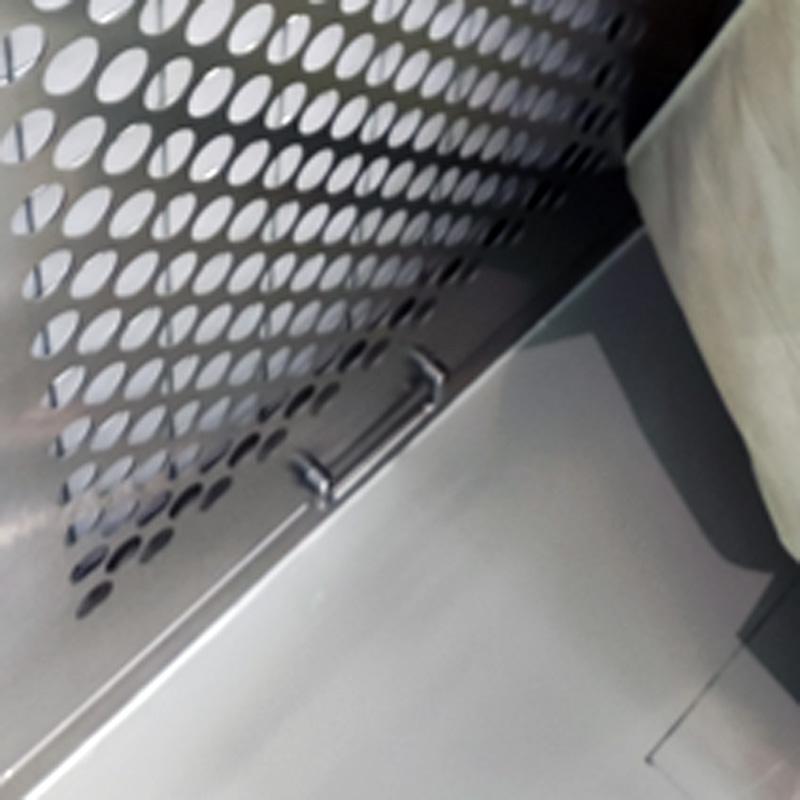
Other's Magnetic Design
Other manufacturers' use of external handles or buckles pales in comparison to Youth's innovative magnetic suction design, which offers superior convenience.
YOUTH's Downflow Booth Manufacturer Features
When it comes to ensuring a controlled and clean environment for pharmaceutical operations, the role of a trusted downflow booth manufacturer becomes indispensable. YOUTH, a leading name in the industry, specializes in creating state-of-the-art downflow booths often utilized in dispensing rooms. These booths offer a precise setting where materials can be handled safely without the risk of contamination. A dispensing room, equipped with booths from YOUTH, a reputable downflow booth manufacturer, ensures that both operators and materials are protected from airborne contaminants. Partnering with YOUTH guarantees that companies uphold the highest standards of product quality and safety.
Related Contents:
- What is the Difference Between a Weighing Booth and a Dispensing Booth?
- Everything You Should Know About Weighing Booths
- The Essential Role of YOUTH Weighing Booths
- The Ultimate Guide to Dispensing, Sampling, and Weighing Booths: Ensuring Precision and Safety with YOUTH
- Cleanroom Booths: A Comprehensive Guide to YOUTH’s Dispensing, Sampling, and Weighing Booths
- Bag-In/Bag-Out (BIBO) Systems: Operation and Maintenance Guide
- Specialized Cleanroom Booths by YOUTH: Ensuring Precision and Safety
- The Best Weighing Booths for Cleanroom Applications
- 5 Innovative Weighing Booth Designs for Your Lab