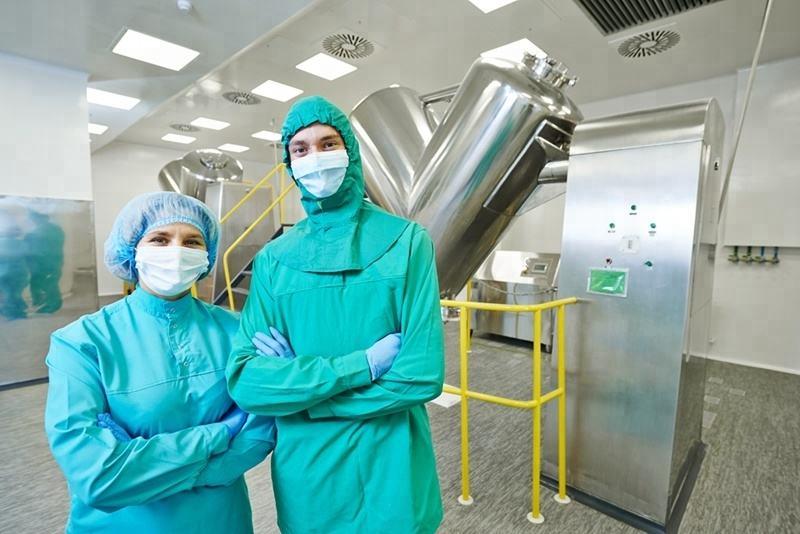
When it comes to industries requiring a high level of cleanliness and contamination control, cleanrooms play a crucial role. Whether it’s pharmaceuticals, biotechnology, electronics, or aerospace, an efficient cleanroom design is essential for maintaining strict quality standards and ensuring the integrity of processes and products. In this article, we will explore the key factors you need to consider when designing a cleanroom to meet your specific requirements.
Understanding Cleanroom Classifications
Cleanrooms are classified based on the number of airborne particles permitted per cubic meter of air. These classifications follow standards set by various organizations, with the most commonly used being the International Organization for Standardization (ISO) classification. The ISO standard outlines particle size limits and the corresponding cleanliness levels required for different applications.
Key Factors in Cleanroom Design
- Environmental Control
Achieving precise environmental control is paramount in cleanroom design. Factors such as temperature and humidity can significantly impact the performance and stability of sensitive processes. Maintaining a stable and controlled environment is crucial to prevent deviations that could compromise product quality or yield. Advanced HVAC systems with efficient filtration are essential for removing airborne particles and controlling temperature and humidity levels within the specified range. - Airflow and Ventilation
Proper airflow and ventilation play a vital role in ensuring uniform particle distribution and minimizing contamination risks. The air change rate determines how frequently the entire volume of air within the cleanroom is replaced. Higher air change rates are required for areas with stringent cleanliness requirements. Additionally, airflow patterns, such as laminar or turbulent flow, need to be carefully considered based on the processes and equipment involved. - Material Selection
The choice of materials used in cleanroom construction is critical for maintaining cleanliness and minimizing particle generation. Specialized flooring and wall systems with low particle release properties, easy cleanability, and resistance to chemicals and abrasion are typically preferred. Ceiling systems with integrated lighting should facilitate maintenance and prevent contamination. Carefully selecting furniture and fixtures that are resistant to chemical agents and easy to clean is crucial to prevent particle generation and facilitate maintenance procedures. - Equipment and Utility Placement
Efficient layout design is essential for optimizing workflow and minimizing the risk of contamination. Proper placement of equipment and utilities, such as air handling units, ductwork, and electrical conduits, should be considered during the design phase. Strategic positioning ensures smooth operations, reduces cross-contamination risks, and facilitates maintenance activities. Service distribution should be planned to minimize the risk of interference with critical processes or compromising cleanliness. - Workflow and Process Considerations
Cleanroom design should also focus on optimizing workflow and process efficiency. Ergonomics plays a crucial role in ensuring the comfort and productivity of cleanroom operators. Designing workstations, seating arrangements, and equipment placement with ergonomic principles in mind helps reduce fatigue and enhance overall efficiency.
Moreover, considering contamination control measures in workflow design is essential. Clearly defined areas for gowning and degowning, proper segregation of different processes, and adequate measures for waste disposal and cleaning protocols are crucial for minimizing the risk of cross-contamination and maintaining the cleanliness of the environment.
- Cleanroom Validation and Monitoring – Cleanroom design is not complete without validation and monitoring procedures. Validation involves rigorous testing and certification of the cleanroom to ensure it meets the required cleanliness standards and performance criteria. Regular monitoring of critical parameters, such as particle counts, temperature, humidity, and pressure differentials, is necessary to maintain control and identify potential deviations.
Continuous monitoring systems equipped with real-time sensors and alarms provide instant feedback on any variations or abnormalities in the cleanroom environment. These systems enable proactive measures to be taken promptly, minimizing the risk of product contamination or process failures.
Conclusion
Designing a cleanroom requires careful consideration of several key factors to ensure optimal cleanliness, contamination control, and operational efficiency. By paying attention to environmental control, airflow and ventilation, material selection, equipment placement, workflow optimization, and validation and monitoring, you can create a cleanroom that meets your specific needs and complies with industry standards.
YOUTH, a leading provider of cleanroom solutions, understands the critical importance of these factors in cleanroom design. With their expertise and comprehensive range of cleanroom products and services, YOUTH is committed to helping industries achieve the highest levels of cleanliness and quality assurance. So, whether you’re in pharmaceuticals, biotechnology, electronics, or any other sector requiring a cleanroom, make sure to consider these key factors and consult with experts like YOUTH to ensure a successful cleanroom design that meets your requirements.
Related Contents:
- Bag-In/Bag-Out (BIBO) Systems: Operation and Maintenance Guide
- The Cleanroom Experience: A Guide to Safe and Efficient Operations
- Understanding the Mechanics of Fan Filter Units: A Detailed Guide
- Exploring the Essential Cleanroom Equipment
- Mastering Cleanroom Gowning: A Comprehensive Guide to Sterile Environments and Contamination Control
- The Clean Team: Key Players in Cleanroom Operations
- Maximizing Cleanroom Efficiency with High-Performance Fan Filter Units
- How to choose FFUs and AHUs?
- Fan Filter Units for Semiconductor Cleanrooms: A Must-Have Solution