What is the VHP Sterilizer for Cleanroom?
VHP Sterilizers: Precision Cleanliness
- Utilizes vaporized hydrogen peroxide for effective sterilization.
- Releases a mist of VHP to eliminate bacteria, viruses, fungi, and other pathogens.
- Commonly employed in medical facilities, labs, and areas requiring high sanitation.
- Capable of sterilizing a variety of materials, such as medical devices, surfaces, and room air.
- Safe operation without leaving harmful residues post-sterilization.
- In cleanrooms, VHP gas circulates to sterilize the entire area.
- Ideal for use in controlled environments to maintain cleanliness and prevent contamination.
YOUTH VHP Generator: Advanced Decontamination
- Developed for equipment internal sterilization and cleanroom decontamination.
- Advanced vaporization process of hydrogen peroxide for complete sterilization.
- Harnesses the enhanced bactericidal and sporicidal properties of VHP at room temperature.
- Extensively applied for sterilizing isolators, transfer hatches, and pass-through chambers.
- Suitable for bag-in/bag-out systems and spaces adhering to GMP standards.
- Ensures a contaminant-free setting for sensitive operations and critical tasks.
Benefits of Cleanroom VHP Sterilizer
Sterilization of Medical Equipment
Cleanroom VHP Sterilizer is a reliable and effective method of sterilizing medical equipment. This technology is crucial in preventing the spread of infections in hospitals and healthcare facilities. The VHP method of sterilization is fast, efficient, and safe for patients and healthcare workers.
Increased Efficiency
Cleanroom VHP Sterilizer is a cost-effective and efficient method of sterilizing surfaces and equipment in cleanrooms. The VHP method of sterilization is fast and requires minimal downtime, which translates to increased productivity.
Cost-Effective
Cleanroom VHP Sterilizer is a cost-effective method of sterilizing surfaces and equipment. The VHP method of sterilization requires minimal maintenance, and the equipment has a long lifespan. The cost of maintenance and support is minimal compared to other sterilization methods.
Comparison of
vaporization and atomization sterilization methods
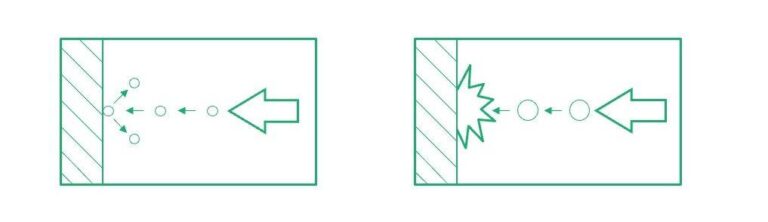
Difference | Vaporized hydrogen peroxide decontamination | Atomized hydrogen peroxide decontamination |
Hydrogen peroxide solution | 30~35% | <8% |
Generated | Flash steaming/heating vaporization | Pressure/ultrasound/rotary flap |
Sterilization mechanism | The vaporization process is controlled below the VHP condensation point to ensure that hydrogen peroxide is in a gaseous state and the gas diffuses to air and surface sterilization | The atomization process keeps small droplets of hydrogen peroxide in the air to achieve the purpose of sterilization |
Uniformity | Uniform distribution and good dispersion performance | Agglomerates into small droplets with uneven distribution |
Control | In the adjustment stage, the VHP concentration is controlled to rise to the sterilization concentration in an increasing form, and the VHP concentration and humidity are strictly controlled during the sterilization stage | With only the atomization effect, it is not easy to achieve precise control |
Sterilization time | It depends on the size of the space | After the disinfection is completed, it needs to stand for about 1~2h |
Discharge time | Hydrogen peroxide remains vaporized and therefore has a shorter emission time. | Disinfectants attached to the surface of objects are not easy to remove. |
Corrosive | The effect on the material is relatively mild | A high concentration of hydrogen peroxide condensed liquid is relatively corrosive on the contact surface |
Bactericidal effect | 6-log | 4-log to 6-log |
Sterilization broad-spectrum | Clostridium difficile, MRSA, VRE, Acinetobacter bauncei and viruses | MRSA and Acinetobacter bougonii, etc |
Surface residue | Lower | Higher |
Consistency of sterilization | Based on the consistency of gas distribution and high diffusivity, good distribution control can be obtained | Varies depending on the uniformity of the distribution of relative humidity, temperature, and concentration in the room |
What are the Differences Between VHP and DHP Sterilizer?
Both VHP and DHP are commonly used as disinfection methods in cleanroom environments, but they differ in their application and delivery.
- Vaporized Hydrogen Peroxide (VHP): VHP involves the generation of a fine mist or vapor of hydrogen peroxide that is distributed throughout the cleanroom space. VHP systems typically consist of a generator or vaporizer that converts liquid hydrogen peroxide into a vapor, which is then dispersed throughout the cleanroom using specialized equipment. The vaporized hydrogen peroxide is effective in disinfecting surfaces, equipment, and the air within the cleanroom.
- Dry Hydrogen Peroxide (DHP): also known as aerosolized hydrogen peroxide or hydrogen peroxide gas plasma, is a method where hydrogen peroxide is converted into a gas or plasma state. DHP systems use specialized generators to produce the gas or plasma, which is then introduced into the cleanroom environment. The gas or plasma interacts with the contaminants and surfaces within the cleanroom, leading to disinfection.
While both VHP and DHP utilize hydrogen peroxide for disinfection, their main difference lies in the state of hydrogen peroxide used (vapor vs. gas/plasma) and the methods of delivery. VHP relies on vaporizing liquid hydrogen peroxide, while DHP involves the generation of a gas or plasma from hydrogen peroxide. The choice between VHP and DHP depends on factors such as the specific cleanroom requirements, the size and configuration of the cleanroom, and the desired disinfection efficacy.
VHP Produces Oxygen-Free Radicals by Vaporizing
hydrogen peroxide solution to act on microorganisms on the surface and environment, which specifically destroys the cell structure and has a broad-spectrum bactericidal effect. It is necessary to control the humidity of the sterilized space to avoid condensation caused by excessive VHP water content.
Dry sterilization process
- Dehumidification – The relative humidity of the space is reduced to the parameter set point so that the air can act as a carrier for hydrogen peroxide gas and the concentration of hydrogen peroxide gas is maintained above the saturated dew point level during the sterilization phase.
- Conditioning – Hydrogen peroxide gas is continuously injected into the dry air stream, replacing the air in the sterilized environment, so that the hydrogen peroxide concentration continues to rise rapidly.
- Decontamination – Maintain the concentration of hydrogen peroxide gas required for sterilization and control humidity during sterilization Aeration Stop the injection of hydrogen peroxide gas, replace the air in the environment, and crack hydrogen peroxide through the lysate to discharge all hydrogen peroxide.
Wet Sterilization Process
- Conditioning – Hydrogen peroxide gas is continuously injected into the dry air stream, replacing the air in the sterilized environment, so that the hydrogen peroxide concentration continues to rise rapidly.
- Decontamination – Maintain the concentration of hydrogen peroxide gas required for sterilization Aeration Stop hydrogen peroxide gas injection, replace the air in the environment, and crack it with the lysate.
Different Sterilization Process
Dry method | Wet method |
Humidity control throughout each stage of the cycle | No need to control humidity |
No supersaturated steam, no condensation generation | The saturated steam is too high, and it is slightly condensed |
Dry gaseous hydrogen peroxide is light in weight, easy to diffuse, and evenly distributed | Microdroplet hydrogen peroxide weighs heavily, is not easy to diffuse, and is unevenly distributed |
The sterilization concentration can be set to achieve uniformity | The sterilization concentration needs to be high and not easy to control |
The process is repeatable | The condensation point is difficult to control and the repeatability is not strong |
Different Removal of Residue and Residue
Dry method | Wet method |
No condensation and faster drainage | Coagulation makes the debris removal process longer than that of the dry sterilization process |
Gaseous hydrogen peroxide is discharged quickly and has no residue | The surface residue is large and corrosive |
Different Verification Method
Dry method | Wet method |
The distribution of biological indicators and the culture results were representative | There are few verification points, and the results are not representative |
Highly reproducible validation | Weak reproducibility |
Different Sterilization Effect
Dry method | Wet method |
Highly permeable, can penetrate HEPA for efficient sterilization | The permeability is poor, and HEPA is difficult to sterilize efficiently |
High repeatability | Weak repeatability |
Good sterilization effect and consistency | The sterilization effect is difficult to standardize, sometimes good and bad, and it is not easy to design the sterilization program |
YOUTH's VHP Tech is Safe, Controllable, and Reliable.
The concentration of hydrogen peroxide is expertly regulated to maintain uniform levels during the entire sterilization cycle, remaining non-condensing to ensure superior compatibility with a wide range of materials. This meticulous control notably reduces the potential for corrosion, safeguarding equipment integrity.
A thorough and methodical assessment of the compatibility with color steel plates is conducted to ensure seamless integration. The results of this evaluation are meticulously compiled into a detailed report, underlining our commitment to quality and material compliance.
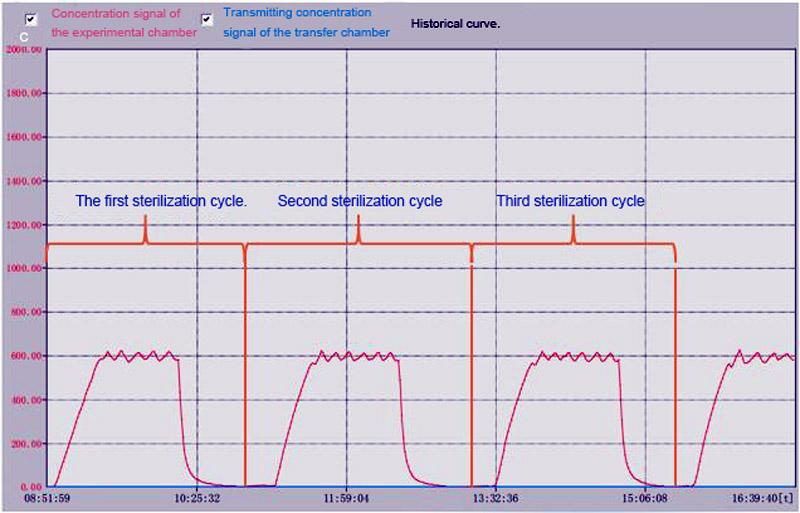
YOUTH’s chosen hydrogen peroxide sterilization method is recognized for its safety, precision, and dependability.
- It is critical to monitor the temperature at the output of the hydrogen peroxide generator, manage integration risks with various environments, and prevent local condensation during operation. Ensuring homogeneous vertical dispersion of hydrogen peroxide is also essential for effectiveness.
- The generator’s outlet design demands versatility to adapt to diverse scenarios and conditions. It should provide options to selectively seal or modulate the aperture based on situational needs, preventing high-concentration hydrogen peroxide vapor from directly contacting color steel plates, thereby safeguarding against localized corrosion.
- Post-sterilization, the degradation process of hydrogen peroxide (including options for catalytic degradation at low concentrations before initiating ventilation) should be chosen with a view towards minimizing risk and promoting eco-friendliness, thereby mitigating the residual discharge’s impact on HVAC systems and the surrounding environment.
Hydrogen Peroxide Drainage (Optional)
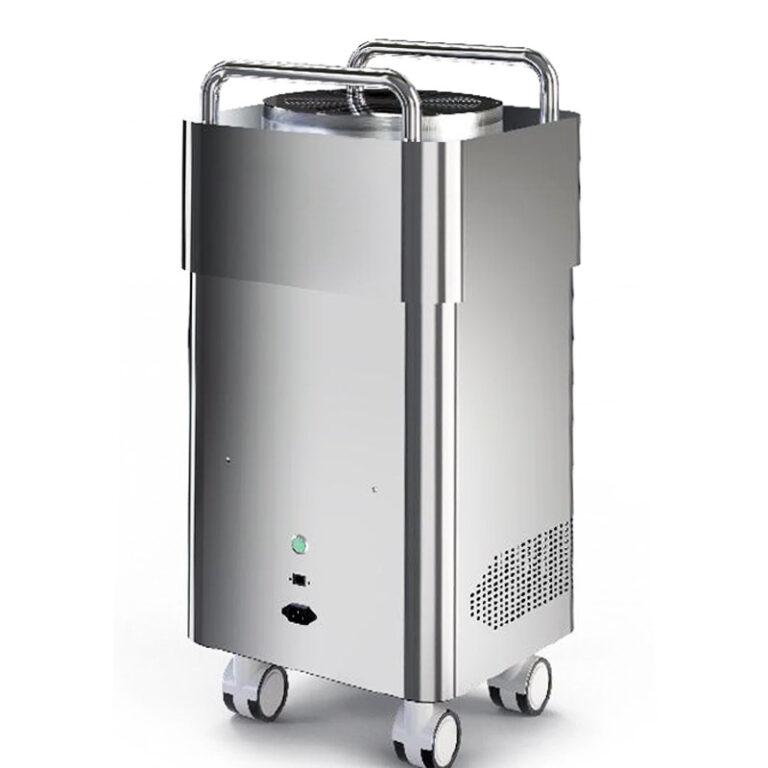
Hydrogen peroxide space decontamination concerns
Robust Compliance with Global Standards
Sophisticated User Access Management
Data Management and Reporting
Innovative Technology and Material Compatibility
Consistency and Stability
Environmental Considerations
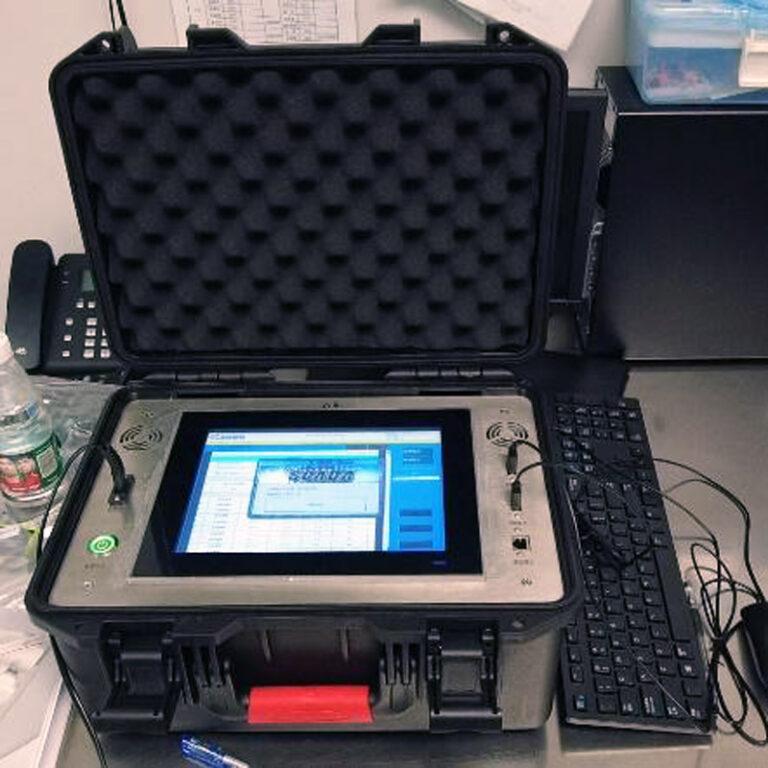
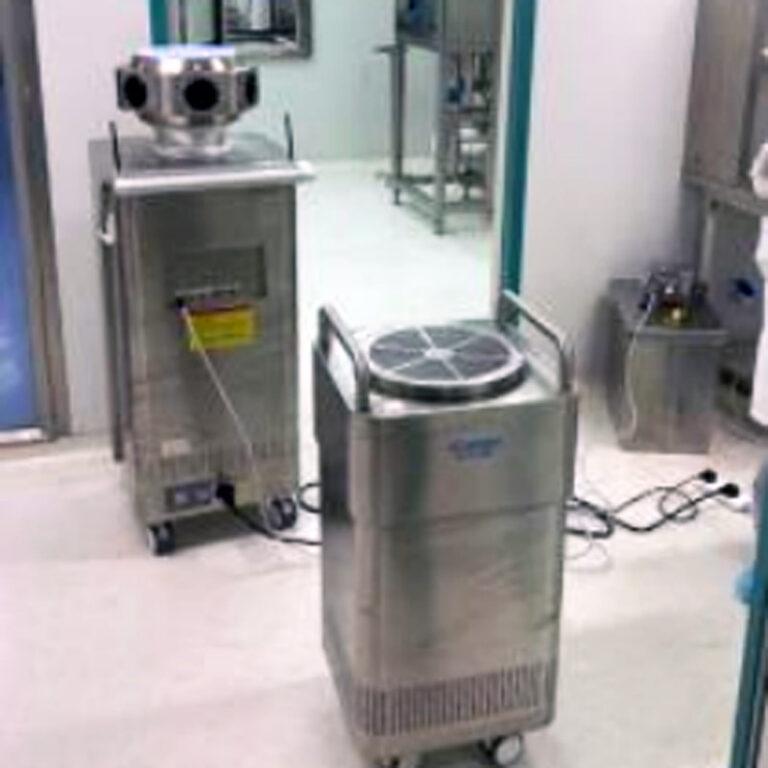
Multiple Equipment Group Control of VHP Generator
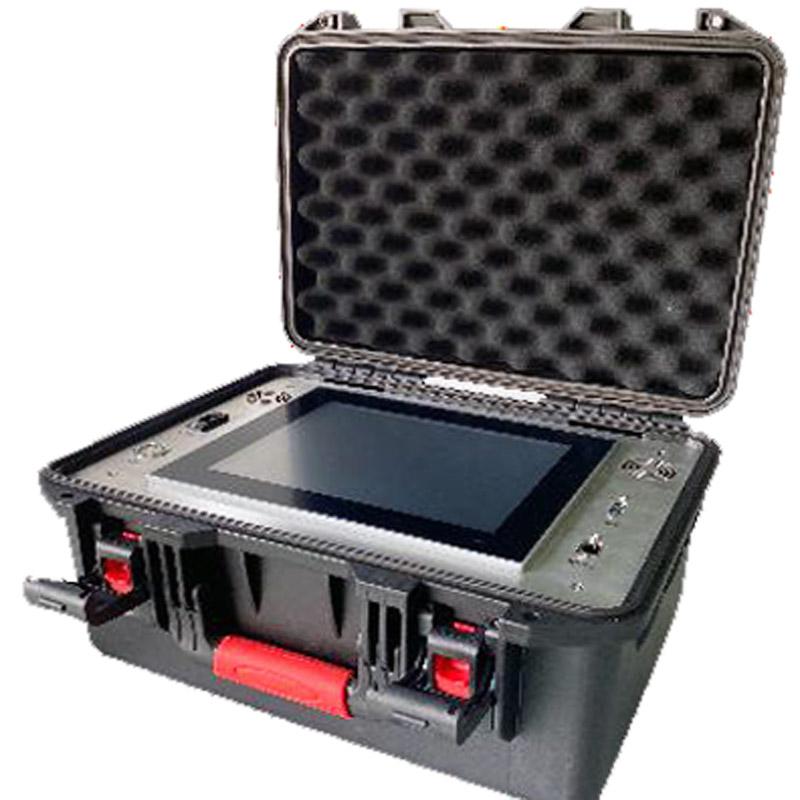
Vaporized hydrogen peroxide generator, supports remote wireless control, and can realize multiple equipment group control, single or multiple equipment simultaneous start and stop control, truly achieving remote supervision. The adjustable nozzle device can spray hydrogen peroxide gas at multiple angles, which can diffuse to the dead corner of the sterilization area to ensure full coverage of the sterilization area.
Related Contents:
- Ultimate Guide to VHP Passbox Cleaning in Controlled Environments
- Ensuring Sterility in Cleanrooms: The Power of YOUTH’s VHP Sterilizers
- Bag-In/Bag-Out (BIBO) Systems: Operation and Maintenance Guide
- The Ultimate Guide to YOUTH’s VHP Pass Box: Ensuring Sterility in Cleanroom Environments
- VHP Pass Box vs. Traditional Pass Box: A Comparative Analysis
- Understanding the Mechanism of VHP Sterilization in Pass Boxes
- Integrating VHP Pass Boxes into Modular Cleanroom Systems
- Cost-Benefit Analysis of Investing in a VHP Pass Box
- The Ultimate Guide to YOUTH’s VHP Pass Box: Ensuring Sterility in Cleanroom Environments